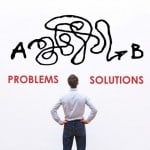
Stand Like a Rock
(Problems and Solutions)
What did American inventor and businessman Charles Kettering mean when he said, “A problem well stated is a problem half-solved”? Framing the problem and pondering solutions can be enlightening, and a great way to learn. This article will pose three problems and offer solutions, as a way to learn by doing.
“I hear and I forget. I see and I remember. I do and I understand.”
Confucius
Beginner’s Problem
Which of the following statements is true about why FMEAs need to be supported by well-understood and communicated principles? (Select all that apply.)
- The entire FMEA process needs to be driven by correct philosophy, meaning that the approach is based on proven principles that support achieving high safety and reliability.
- The essence of “guiding principles” is the specific procedure that the FMEA team follows once the FMEA has begun.
- If one’s approach to doing FMEAs is based on incorrect objectives or wrong principles, then the results will be less than desired.
- Having the right philosophical approach to doing FMEAs applies to System and Design FMEAs, but not to Process FMEAs.
- The entire FMEA process needs to be driven by correct philosophy, meaning that the approach is based on proven principles that support achieving high safety and reliability. (True)
- The essence of “guiding principles” is the specific procedure that the FMEA team follows once the FMEA has begun. (False. The FMEA guiding principles are the foundation for excellent FMEAs. The procedures are the detailed steps of how to implement FMEAs.)
- If one’s approach to doing FMEAs is based on incorrect objectives or wrong principles, then the results will be less than desired. (True)
- Having the right philosophical approach to doing FMEAs applies to System and Design FMEAs, but not to Process FMEAs. (False. Having the right philosophical approach to doing FMEAs applies to all types of FMEAs.)
Intermediate Problem
Study the following FMEA excerpt for a projector lamp:
[click to enlarge]
Which of the four recommended actions in this excerpt are supportive of a philosophy that focuses on prevention? Why?
Advanced Problem
You are asked to lead an FMEA team to perform a Design FMEA on the new bicycle braking subsystem. You understand that FMEAs are a team-based activity, and have identified a cross-functional team of 6 people. The proper preparation tasks are completed and you schedule the first team meeting. Only one person shows up, in addition to yourself. What should you do and why?
As covered in this article, FMEA is a team-based activity. There are many reasons that FMEAs need to be performed by the right team of subject matter experts. Here are three such reasons.
- People have “blind spots.” A well-defined cross-functional team minimizes the errors inherent with “blind spots.”
- The FMEA analysis requires subject-matter experts from a variety of disciplines to ensure incorporation of all necessary inputs into the exercise, and that the proper expertise is applied to the design or process being analyzed.
- One of the indispensable values of an FMEA is the cross talk and synergy between subject-matter experts that occurs during the meetings. Well-defined groups can discover things that individuals often miss.
I would not suggest going forward with an FMEA meeting when the primary team members do not show up. There may be some tasks that can be supported by one or two people, such as improving the FMEA Block Diagram, or identifying candidate functions from the product technical specifications. However, the procedure of FMEA should be done with the team present in the room, being led by a skilled facilitator. Before the next FMEA meeting, management should be consulted to obtain their support in getting full attendance at future FMEA meetings.
Next article
What are the most important factors for success in FMEA applications? This topic will be explored in the next article titled “FMEA Success Factors.”
Hi Carl,
For FEME design change is applicable?
If design is changed after initial RPN calculation then can we change severity level in second step?
Regards,
Roopesh
Hi Roopesh,
If by “second step” you mean the final RPN calculation, the answer is a qualified “yes.” If the FMEA team believes the design change has changed the severity of the effect for a given failure mode, they can enter the modified severity rating in the FMEA worksheet. In this case, the design change should be reflected in the FMEA “recommended actions” and “actions taken” columns, and the modified severity rating should be entered in the “severity revised” and corresponding “RPN revised” columns.
Please let me know if this answers your question.
Thanks.
Carl