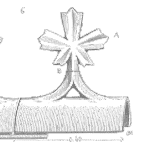
Plant compressed air waste control. Every compressed air system will eventually develop leaks from connectors and redundant pipelines. Compressed air is very expensive to make. It is necessary to institute regular inspections for air leaks and fix them immediately.
Keywords: pressure loss, energy loss, air compressor, pressure switch.
Air Leaks are Everywhere
Air leaks in a compressed air system can be at numerous locations and for numerous reasons. Below is a list of the many ways and places air leaks can occur:
- Threaded joints cross-threaded, with mismatched threads
(e.g. BSP forced into NPT connections) loose threads,
unsealed threads, worn threads. - Loose or mismatched flanges.
- Broken push-in air fittings or damaged plastic hose ends.
- Bent over ends on redundant pipes.
- Plastic lines to actuators cracked when bent over to isolate actuated
valves during maintenance. - Cracked or squashed plastic pipe or metal tubes.
- Ultraviolet light damage to plastic pipes from sunlight.
- Chemical attack or corrosion.
- Plastic lines burnt by weld splatter.
- Plastic lines melted on hot equipment or pipes.
- Valve stems and valve actuator stems.
- Connections to equipment.
- Valves that no longer seat properly.
- Valves left partly open.
- Failed automatic drains.
- Leaking air receiver doors and attached fittings.
- Passing pressure relief valves.
Instigate Regular Inspections
The only way to stop air leaks is to find them and fix them. One method is to get a spray bottle of soapy water and walk the pipe work testing every joint and connection by spraying, or wiping, the soapy water onto it and looking for bubbles forming as the air leaks out. If the leak is substantial it can be heard. Highly sensitive listening devices are also available but these are expensive and more time consuming than the soapy water method.
A full inspection of the compressed air system should be done every twelve (12) months. Operators and maintainers need to report every air leak they see and raise a work order to repair it.
Instigate Good Standards
Using good engineering, installation and maintenance standards and practices can prevent a lot of air leaks. Critical air supply systems should be fully welded. Important connections and pipes to equipment should be of stainless steel tubing and ferrule cone connectors or pressure-on-face sealing connectors. Mixing fittings and materials must be prevented. All connections should be in a position that can be easily reached for inspection and repair.
Train installers in the proper methods of sealing threads. Review old engineering piping standards and update them with better practices and then reissue them to the engineers and maintenance people. Explain the changes and train people in their use.
Reduce The Air Pressure
In order to minimise the cost of air leaks, run the compressed air at the lowest pressure possible. Usually the air compressor has a pressure switch that covers a range of pressures. With approval from Operations conduct trials to see the effect on equipment of using a lower set pressure and set the switch to the lowest acceptable operating pressure.
Mike Sondalini – Equipment Longevity Engineer
We (Accendo Reliability) published this article with the kind permission of Feed Forward Publishing, a subsidiary of BIN95.com
Web: trade-school.education
E-mail: info@trade-school.education
If you found this interesting you may like the ebook Process Control Essentials.
Leave a Reply