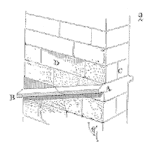
Fundamentals of Physics of Failure
podcast episode
A good physics of failure (PoF) model helps you understand the impact of stresses on the time to failure distribution for a specific failure mechanism. Let’s discuss PoF models, including how to create and use them effectively.
The development of PoF models got off to slow start in the 1960s. Recently, scientists and engineers have developed numerous PoF models for many of the common failure mechanisms we face in our products.
Let’s define a PoF model and how you can create a model for use with a specific failure mechanism. Plus, let’s explore how to find and adapt models found in the literature.
While not every failure mechanism will have a suitable model, those that do provide a quicker analysis of failure risks for your product. Your team can consider design changes, changes in material, assembly changes, or changes to environmental protection and quickly assess the impact (good or bad) on the expected time to failure distribution.
A mixture of models allows you to model the many competing threats to your product’s successful operation over time. Combining these models with differences in use or environmental stresses across your customer base permits modeling the effective field reliability performance.
Let’s consider PoF models, how to use them, plus how to create them, as a central element of your reliability program. We’ll discuss a range of models and where you can find more to help describe your salient failure mechanisms.
This Accendo Reliability webinar originally broadcast on 8 January 2019.
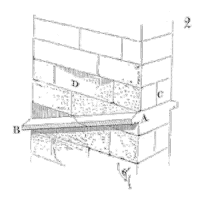
- Social:
- Link:
- Embed:
To view the recorded video/audio of the event visit the webinar page.
The Physics of Failure (PoF) methodology is founded on the conviction that failures are governed by fundamental mechanical, chemical, electrical, thermal and radiation processes. These processes are initiated when the applied stress exceeds the material strength. Using PoF methodology provides for a systematic approach to reliability assessment, which involves virtual qualification, accelerated testing, and screening development, and allows for the design and manufacture of quality products. Relevant attributes for this assessment include dominant failure mechanisms, the stress drivers for failure, and a pareto ranking of the time to failure due to the dominant failure mechanisms
The PoF aapproach proactively incorporates reliability into the design process by establishing a scientific basis for evaluating new materials, structures and electronics technologies. Information to plan tests and screens and to determine electrical and thermo-mechanical stress margins are identified by the approach. PoF encourages innovative, cost-effective design through the use of realistic reliability assessment. Generic failure models are used by physics of failure, which are as effective for new materials and structures as they are for existing designs.