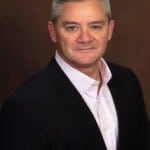
Moving to Proactive Maintenance with Scott Kelley
In this episode of the rooted in reliability podcast, the guest Scott Kelly explains the sixth cell of the hexagon of Plant-Hexcellence Model. All the cells of this model are linked together so that every cell is critically important to get good results from your plant. But there are always prioritized standards for different people working in the organization and most of them consider the proactive maintenance above all as it’s the best way to save both time and money. Basically, it is a strategy through which you plan your asset management process from the very start till the end by looking at the design of the machines, construction, visual inspection, and so on.
Now, most of the organizations don’t plan for long-term preventive and proactive maintenance—considering the earlier one is only a part of the latter one. They have to be made for the whole life cycle of the equipment as a failure can occur at any time. The organizations need to focus on the mitigation strategies along with operational and management costs of the equipment throughout their lifetime. Now there are some facets that this cell is made up of just like the rest. These facets include:
- Reliability Availability Maintainability Model A.K.A RAM which is made of modeling diagrams, statistical methods, and so on. These diagrams—designs or tree diagrams—are given as an input to the simulation software that tells you the true integrity of your whole reliability programs and systems that you have put in place according to your plan of action.
- Then comes the Weibull analysis that is based on your failure and equipment data that you have in the form of registers, diagrams, and field data obtained by different means. These statistical techniques actually give you insights about your decision making systems.
- You also have to assess your plans relevant to your cost and equipment management and make it consistently better by reassessing again and again after some intervals.
- After that preventive maintenance comes along where you try to do things as right as possible as mistakes lead to failure. You have to check the installation, alignment, and such things that stop the error from occurring in the first place. All of this can only be achieved if you have done your maintenance in perspective with the proactive maintenance.
- The last thing to do using a proactive approach is the predictive maintenance that comes as a decisive factor and can only be done correctly via visual inspection and evaluation. Vibration analysis is also a part of this activity but it doesn’t need to be done on everything. It should just serve the purpose and your needs. You also need to take thermographic measures of your machines along with performing a tribology and ultrasound inspection as well to make sure the defects are minimum.
The start-up and shut-down of the equipment at the right time also helps a lot in this endeavor of proactive maintenance along with doing a motor current analysis every now and then.
Eruditio Links:
- Eruditio, LLC
- A Smarter Way of Preventative Maintenance – Free eBook
- Maintenance Planning & Scheduling: Planning for Profitability Video Course
- Plant Hexcellence Article on Performance
Geometric Reliability Links:
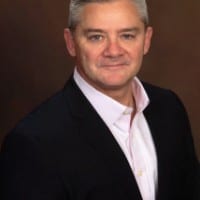
- Social:
- Link:
- Embed:
Rooted In Reliability podcast is a proud member of Reliability.fm network. We encourage you to please rate and review this podcast on iTunes and Stitcher. It ensures the podcast stays relevant and is easy to find by like-minded professionals. It is only with your ratings and reviews that the Rooted In Reliability podcast can continue to grow. Thank you for providing the small but critical support for the Rooted In Reliability podcast!
Leave a Reply