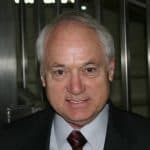
Reliability with a Best Practice Organization with Heinz Bloch, Part 1 of 2
The leap towards becoming a best-in-class company is challenging. If you’re like most people, you might have wondered the difference between best in class companies and typical companies as far as reliability practices are concerned. While it’s true that there are other elements that are at play that make for a best-in-class company, one can’t deny that maintenance and reliability is one differentiating factor and a critical element at that.
Heinz Bloc, with his more than 40 years of industrial experience and having been immersed to best practice organizations himself, gladly shared the steps that companies can take to improve performance and aim for world-class status in this 2-part podcast episode.
But what are a best-in-class companies? How about world-class companies? And most importantly, are all large companies necessarily best-in-class? Let’s quickly define each of these terms to set the tone for this discussion.
According to this definition, best in class means the highest current performance level in an industry, used as a standard or benchmark to be equaled or exceeded. Also called best of breed or best in practice. On the other hand, world-class is defined as goods, services, and processes that are ranked by customers and industry-experts to be among the best of the best. This designation denotes standard-setting excellence in terms of design, performance, quality, and customer satisfaction and value when compared with all similar items from anywhere in the world. One can safely say, therefore, that being best in class is a step towards becoming world-class, and it doesn’t always follow that if you are a big company, you are the best in class or you’re your product/service, even your processes, are world-class. Throughout this podcast, however, we shall use the term best in class to refer to best reliability practices.
Also, we hear the terms “maintenance” and “reliability” frequently in the industrial space. Everyone in a plant should understand the definition of maintenance and reliability and what they mean to the success of the company. Maintenance is about efficiency while reliability is about effectiveness. To state it a different way, you cannot focus on doing the right job (reliability) without doing it the right way (maintenance). But the more important point isn’t how they are different, but how they are the same! The ultimate goal of maintenance is to provide optimal reliability which meets the business needs of the company. Reliability is probability or duration of failure-free performance under stated conditions. Many companies focus on fixing equipment when it has already failed – not on ensuring reliability, and avoiding failure.
As maintenance and reliability evolved over the years, so too are their structure and specialization. Perhaps the term reliability was not used in the same context as it is today. Yet, it was unconsciously practiced since maintenance at that time had the task of maintaining the equipment and dealing with issues that were technically outside of maintenance definition such as upgrading equipment beyond what it was inherently capable of. In the 1960s, reliability department did not normally exists in an ordinary or average refinery. Instead, they have a designated individual to equip maintenance department and identify when an upgrade was possible. Today, there are many instances of separation between maintenance and reliability departments, and the two may operate as separately and independently of another in terms of where and how they report to, depending on the size and maturity of the organization. In large companies, you have a separate reliability group because problems are a combination of equipment, operations, people, and other factors. This group might not report to operations or maintenance, but to the mill manager or independent engineering manager. Maintenance focused on here and now and restore the asset’s current condition while reliability is more focused on what needs to be done to prevent or eliminate failures and defects from occurring again.
When is typically reliability steps in? In a best practice plant, for instance, when a pump frequently failed over several years and finally failed for the second time in a 12-month period, this is no longer the jurisdiction of the maintenance department because the pump has proved itself to be frequently failing pump. This pump and it’s upgrade is now under the full jurisdiction of the reliability department, and the reliability department is ready to single out certain pieces of equipment and to be ready to implement certain upgrades. It’s now reliability’s responsibility to sort that out, to implement corrective actions, and to prevent that such issue from occurring again, provided the issue was sufficiently communicated and ample warnings were given ahead of time to reliability department by the maintenance team. So, that example highlights how the two departments function separately and clearly delineates where their responsibilities are.
Normally in best in class companies, reliability department has in place already a roadmap as to what they will do and have pre-purchased the possible solutions. After a recurring issue has been reported a few times and ruled out that the cause was due to conventional lubrication which simply has not been adequate and has allowed this frequent bearing failures, reliability already know what type of lubrication method to switch over to. So this is an example of how prepared reliability department will be to step in and to not just recommend upgrade but to really implement this upgrade and to work with whoever is on the outside or inside of the company to physically install these parts and to install and recommission these parts correctly.
Apart from autonomy and independence that are seen from the two departments, the best in class companies also adopt the most effective managerial and people-centric approaches to build a culture of collaboration and teamwork. You don’t normally see finger-pointing and passing the blame from one person to another or from one department to another. To become truly world-class, everyone in the organization needs to be involved, to be empowered, even cross-trained, so that when there is any business urgency and some departments have to switch hats, they can still operate as normal. In addition, in an organization with several layers of supervision, whenever one has to explain his/her observation, she/she has to go through the layer of authority that mostly resulted to message not reaching the right people or that the next level supervisor couldn’t do much about since the supervisor is 2 or 3 layers below. In best of class companies, people are allowed access to the top management so ideas and suggestions are channeled to the top.
Simply put, it’s all about cross-functional collaboration, teamwork, accountability, and having that vision moving forward. The role and management style must adapt to the skill level of the people. If craftspeople have a high level of skills, they need support in the form of priorities, planning, and scheduling instead of detailed technical instruction. Both craftspeople and supervisors must realize that people skills are more important than technical skills. When immediate superiors, even coordinators, support people through good planning and scheduling of work, identifying individual training needs, organizing this training, coaching root cause failure analysis, and other empowering tasks instead of spending much time instructing them, this promotes a thinking and problem solving organization instead of a reactive one.
Similarly, top management should be advocates themselves. Reliability is, and must be treated as, a holistic organizational issue where all functions and all employees, from the CEO to the newest hire on the factory floor, have critical roles to play. Executive buy-in is not enough. Executive support is just as important, if not crucial, to promote a culture of collaboration and teamwork. If everyone in the organization truly understands and appreciates operations, maintenance, and reliability principles, they can live in each other’s shoes and that’s where learning and appreciation comes from.
Failure analysis has gone through some changes as well over the years. Management changes can also have some drastic changes on continuity on the implementation of failure analysis practices. Some typical companies if they changed management, they normally abandon the previous implementation and default to what being recommended by the new management resulting to initial practices being abandoned. In best of class companies, there is sustainability regardless of the management and what has been initially implemented is continuously adopted and improved, given it was working practice. How it’s working effectively for best in class companies is that the preliminary review or assessment starts from the lowest ranks and will just have to escalate if further help is needed. This provides empowerment even to the rank-in-file employees.
Failure analysis will not be at the top-end of chain of achievability without these elements of openness and internal enablement. After all, the best practice failure analysis is one in which the life and behavior of the machine was influenced by at least three job functions simply summarized as PMT (Process Person (Operations), Maintenance, and Technical Person) who systematically work to identify root causes of the problem.
Eruditio Links:
- Eruditio
- HP Reliability
- A Smarter Way of Preventative Maintenance Free eBook
- inspired Blended Learning (iBL®)
- James Kovacevic’s LinkedIn
Heinz Bloch Links:
- Personal Website
- Email: heinzpbloch@gmail.com
- Recommended Book: Petrochemical Machinery Insights
- Other Books by Heinz P. Bloch
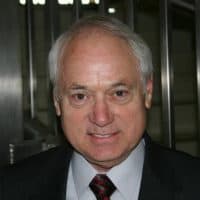
- Social:
- Link:
- Embed:
Rooted In Reliability podcast is a proud member of Reliability.fm network. We encourage you to please rate and review this podcast on iTunes and Stitcher. It ensures the podcast stays relevant and is easy to find by like-minded professionals. It is only with your ratings and reviews that the Rooted In Reliability podcast can continue to grow. Thank you for providing the small but critical support for the Rooted In Reliability podcast!
Leave a Reply