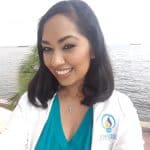
Lubrication with Sanya Mathura
In mechanical fields like automotive, oil and gas, power generation and aviation industries, lubricants play a critical role in maintaining equipment reliability. They consist of both oils and grease.
In this episode, Sanya Mathura of Sustainable Reliability Solutions shares her thoughts on why and how organizations can foster an active approach to lubrication.
The episode highlights are:
- Why organisations should be concerned about lubrication
- How to identify degradations in lubricants
- Common types of lubricant degradation
- The impact of failing lubricants
- Best practice for storage and testing lubricants
Why organizations should be concerned about lubrication
Often, lubricants will change their physical and chemical nature before the actual failure occurs. Once a failure occurs, the two most effects are:
- Unplanned downtime as a result of lacking detection mechanisms
- Incurred costs related to unexpected stoppage
It is therefore important for facilities to understand and communicate these effects in order to take corrective action.
How do I identify lubricant degradation?
Common telltale signs of degradation are slightly different in oils and greases. For oils, darkening is a common indication of degradation. Greases on the other hand show inconsistency and noticeable oil separation.
However, to verify the extent of degradation, it is recommended to carry out more analyses in the lab.
Types of degradation
Lubricants will degrade according to the application that they are serving, as well as the conditions they are exposed to. Degradation in automotive applications might differ slightly from those in power plants.
The six types of degradation are:
1.Oxidation
This is the most common type across all applications. It occurs when antioxidants in the lubricant start to wear off and acidity increases. Visible signs of lubricant oxidation include a sludgy look or fell, as well as varnishing. When undergoing lab tests, you will also notice an increase in viscosity.
2. Thermal breakdown
This breakdown is characterized by lower viscosity. The main cause of thermal breakdown is high operating temperatures which trigger a chemical reaction that affects viscosity.
3. Microdieseling
This effect comes as a result of micro-ignitions when unwanted bubbles inside a hydraulic lubricant are subjected to high temperatures.
4. Additive depletion
5. Electrostatic spark discharge
6. Contamination
How lubricant degradation affects organizations
Depending on the industry, or nature of the operation, the effects of degradation take on different forms. Oxidation and thermal degradation are the most common types.
In a power plant, for example, the effects of oxidation will make solenoid valves sticky and prevent optimum operation. The result is unexpected downtime which could come at the expense of generation uptime. In a car, for example, oxidation simply alls for an oil and filter change.
Contamination is also a common effect. However, the causes might be either external or internal. External causes can come from the action of an outside party, like a supplier. Internally, processes like storage conditions can also lead to contamination.
How do we test for degradation?
At a basic level, it is advisable to test your lubricants each month. Depending on your operational needs, tests are not limited to:
- Viscosity
- Acidity
- Moisture content
- Color
Beyond the basic monthly tests, you should have your customized test schedule. This schedule should be subjective to the industry you operate in. Records of these tests should also be kept. Additionally, data analysis can also be done to monitor signs of degradation.
Storage considerations for lubricants
A lubricant will slowly start losing its lubrication power as soon as it’s manufactured. Organizations become responsible for their degradation control as soon as they receive and store the lubricants for use.
Consider the following pointers to help you store lubricants better:
Store in the right conditions. Check the manufacturer’s recommendations on the optimum storage conditions. At the very least, keep lubricants away from water. Greases need to be kept away from high heat and light areas.
Check the lubricant expiry date.
The expiry date tells us of the date before which we should put the lubricant to use. We can treat it as the shelf life. Shelf life will be a significant contributor to additive degradation if it is exceeded. Service life, on the other hand, refers to the actual usage period of the lubricant. It is not uncommon for the service life to be longer than shelf life.
Best practice to ensure lubricant longevity
Observe these tips to get the most of your lubricant and equipment:
1. Train your personnel
It is crucial for the operators to understand what defective lubricants can cause to the company and market. They should be at the forefront of selecting lubricants at their best state.
2. Perform regular health checks on lubricants
Whether it’s the storage tanks or equipment behavior, regularly check the state of lubricants in their usage. The information gathered can be helpful in pointing on an imminent performance drop.
3. Prioritize the expiry date
As much as we observe the common analogy of First-In-First-Out (FIFO), you should be guided by the expiry date. This strategy will help you avoid issues of additive degradation
4. Do basic tests frequently
Understanding the lubricant health before the application will help you anticipate any performance drops.
The main takeaway from this episode is that you need to educate your staff on lubricant importance. You should also check your lubricant periodically to ensure it is performing as expected. Or as Sanya says:
“Listen to your lubricant!”
Eruditio Links:
Sanya Mathura Links:
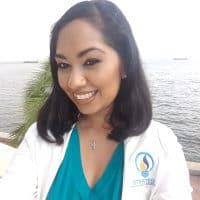
- Social:
- Link:
- Embed:
Rooted In Reliability podcast is a proud member of Reliability.fm network. We encourage you to please rate and review this podcast on iTunes and Stitcher. It ensures the podcast stays relevant and is easy to find by like-minded professionals. It is only with your ratings and reviews that the Rooted In Reliability podcast can continue to grow. Thank you for providing the small but critical support for the Rooted In Reliability podcast!
Leave a Reply