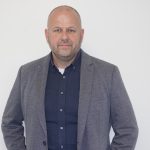
PDM with Martin Blenkers
All through Europe, America and other emerging economies, the new wave of industrial technologies is bringing a fundamental shift to how we approach operations. With tools like artificial intelligence and machine learning, reliability and maintenance as we know it is being curved in vastly different ways. Martin of Uptime Works helps us get up to speed with how we can start leveraging predictive maintenance strategies to improve productivity and cut on costs.
The points addressed in this podcast highlight:
- What Predictive maintenance is
- The importance of predictive maintenance (PDM)
- Technologies that can strengthen successful PDM
- Major considerations before getting into PDM
Definition of Predictive maintenance
In simple terms, predictive maintenance refers to the practice of using technology tools to monitor the condition of an asset in order to see signs and symptoms of failure well in advance. The data sources for this continuous practice are both process and condition-based data.
Process data refers to the performance metric collected from a piece of equipment. Examples could be flowrate information from a pump, or power drawn by a compressor. Condition-based data, on the other hand, refers to data points around an asset that indicate its state. Examples could be oil parameters for a mechanical arm or vibrations from a motor.
A combination of these two layers of data is being increasingly collected and assessed to paint a better predictive maintenance picture of assets. This trend of adoption is quickly spreading across the world.
Importance of Predictive Maintenance
Because of a rapid decrease of hardware vis-a-vis a rise in performance, organizations are now more empowered to install more data collection devices around their processes. The devices are data generators for both process and condition-based data. Depending on only one of these data layers is not bringing the richness in insights that could be derived from a combination.
However, data quality still remains to be a problem with building a predictive maintenance program. There is still an unclear understanding of what data to collect and the specific types that will mean the most to an organization. organizations that are now allowing third-party professionals to analyze their (proprietary) process data are the ones taking advantage of new software capabilities like machine learning.
Technologies to help in building a holistic predictive maintenance program (PDM)
Exploring the following considerations might help your organization’s PDM strategy
Leveraging visual analysis
Visual inspection is still underrated by today’s standards. Periodic visual analysis will not only help us get a bigger picture, but it also influences where we should be focusing our data collection tools
Getting data in one environment
A common challenge with dealing with hardware providers is that they will often come with their proprietary software. The arising challenge is that facility operators have to constantly swing from one app to another just to check data. The analysis becomes uglier if people have to download data from one platform to Excell before plotting trends.
Having a way to integrate these data generation sources onto one platform creates huge time savings and makes analysis easier.
The people factor for holistic PDM practices
People are at the center of this technology change. A few considerations to take care of are:
Ensuring people are on the field as little as possible
The end result is that people spend more time creating value out of data, rather than collecting it on the field. To achieve this, ensure that you have implemented a well-planned data collection strategy, which covers all critical data points and s run on reliable hardware.
Make technology that is easily adopted by less trained technicians and engineers
Because of the fast change in industrial technologies, not everyone is able to invest and learn about the latest. Instead of organizations relying on expensive expertise, it is more economical to pick technologies that are easy for the technical team to adopt. This means that the technology should not require a lot of new (or proprietary) knowledge to implement and have plenty of visual aids.
Foundations to put in place before implementing PDM
Believe in it
Key to any technology implementation is the belief that it is for the good of the organization. The buy-in has to be from as many people across the organization as possible. There also has to be an understanding that the investment cost will be substantial, and that the benefits will take some time before coming around.
Get the basics right
Even before looking at adopting any new technologies, consider the current state of affairs with your processes. Ensure they are efficient, clear and easy enough to rely on. An example could simply be having your housekeeping in check, adhering to visual inspection routines, observing lubrication standard operating procedures (SOPs).
Start small
Holistic predictive maintenance does not have to take a grandiose start. Because it takes a while before you see the results. A better approach would be to start small, and by tackling the low hanging fruits. This way, people can quickly see the results and firm their buy-in.
How to take a holistic approach to PDM
As mentioned, the major challenges would be addressed by:
- Having the data collected into one environment for easier analyses and comparison
- Designing a dynamic database that can be later expanded to handle new data sources
- Reducing the need to go to the field
- Having a good command of the basics
Benefits of a holistic approach
Quite simply, you stand to uncover new insights about your processes. Being able to combine condition-based and process data opens new avenues for analysis and understanding of your assets. This opportunity then allows your team to start eliminating false alarms and reducing reactive maintenance time.
One thing that makes the biggest difference for holistic PDM
This is the belief that what is being implemented is for the good of the company. If there isn’t enough buy-in from the staff, then it would mean that you have not understood their needs correctly.
Communication of the potential transformation and what’s in it for the implementers will also help them support the adoption.
Key takeaway
- Using the experiences of other companies is afters way of learning from their successes and failures.
- If possible, learn as much as possible from a service provider before investing in the technology
- Use events to connect with other providers and hopefully people who have also implemented holistic predictive maintenance strategies before
Eruditio Links:
Martin Blenkers Links:
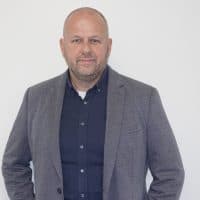
- Social:
- Link:
- Embed:
Rooted In Reliability podcast is a proud member of Reliability.fm network. We encourage you to please rate and review this podcast on iTunes and Stitcher. It ensures the podcast stays relevant and is easy to find by like-minded professionals. It is only with your ratings and reviews that the Rooted In Reliability podcast can continue to grow. Thank you for providing the small but critical support for the Rooted In Reliability podcast!
Leave a Reply