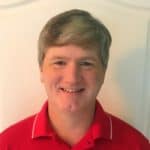
Reliability Career with Tim Holmes
We’re excited to have Tim Holmes joining us. Tim’s presented at conferences and worked with SMRPs. He’s also DuPont Operations’ principal internal corporate consultant for reliability and maintenance engineering. Before that, he was involved in maintenance and reliability as well as Six Sigma. He’s actively involved in SMRP since 2011. Tim’s a Carnegie Mellon mechanical engineer and engineering in public policy graduate with a total experience of 33 years in the field.
Tim will give us insight on:
- How did he get pulled into maintenance and reliability?
- Roles that influenced Tim’s view on maintenance and reliability
- What is the difference between maintenance and reliability engineering?
- Which roles allowed him to better understand maintenance and reliability?
… and so much more!
How did he get pulled into maintenance and reliability?
Tim left college wanting to be a plant manager. But the engineering manager that hired him after college was a chemist by background, rather than a maintenance and reliability person. He had a lot of knowledge on manufacturing and foresight to see what was coming in technology, and maintenance and reliability. This made him hired Tim and trained him on the relevant technologies. He taught him in a way he could implement the lessons across his site. Tim continued to embrace the technologies and even championed for their use throughout DuPont.
Roles that influenced Tim’s view on maintenance and reliability
For the first seven months of his career, Tim worked as the lone mechanical engineer. He was supporting the maintenance organization in the plant alongside chemical engineers who supported the production side. While there, he learned:
- The site
- About the business
- DuPont’s safety expectations and principles
- How to use the process history in other operations and tools
Later, Tom moved out to the plant to become a maintenance engineer for one of the four process areas in the plant. He was placed at the beginning of the pigment process to support three mechanical crews and one electrical and instrument crew. He handled raw materials. There were solids like coke and ore. There were also chemicals like chlorine. This gave Tom experience in solids handling and handling of toxic materials.
Since other mechanical engineers were running capital projects, Tom found himself supporting over a dozen maintenance crews and nearly 200 maintenance technicians. He learned about:
- Predictive maintenance
- Laser alignment
- Balancing
- Lubrication
- Pipe Codes
- Welding
- Non-destructive testing
After about eight months he became a maintenance supervisor. For the first two months, he worked 12-hour shifts. He led four mechanics and one instrument electrical technician during those shifts. Then on the off shifts, they maintained the entire plant. One of the critical roles Tim got with the job was being the on-scene emergency response coordinator in case of a fume release or fire.
In the last seven months as a supervisor, he had a day crew. He supervised the raw materials area because the supervisor was on special assignment. So, Tim took over his crew, becoming the site’s official maintenance engineer. In this role, he:
- Certified in many of the predictive maintenance and non-destructive testing technologies
- Led those technologies across the entire site by working with mechanics from each maintenance crew to do predictive maintenance in their areas.
This was a challenge since Tim worked with a vibration guy in the plant on one day. The next day he’d go work with another guy in another area of the plant. It was an extremely dispersed program that didn’t work well.
So Tim requested the leadership to provide him with two full-time mechanics for better results. He got three as well as an instrument and electrical technician. A fourth mechanic was added later based on the progress that the leadership saw. Tim’s team:
- Implemented vibration analysis across the plant
- Implemented Laser alignment across the plant
- Pulled in all the field balancing
- Started to pull oil samples
- Started to pull in and modernize the non-destructive testing programs using scan technology
While the rest of the team handled the predictive maintenance and NDT, Tim expanded the role. That’s by adding to his skill base:
- Root Cause Analysis
- Reliability Centered Maintenance
- Total Productive Maintenance
- Autonomous maintenance
This is what caused the transformation from a maintenance engineer to a reliability engineer. He adopted the title of a site reliability engineer.
What is the difference between maintenance and reliability engineering?
Maintenance engineers support the maintenance crews. They do things like:
- Helping to set up maintenance plans
- Provide technical assistance for maintenance work
- With reliability engineers, they try to work ahead of the problem. Instead of repairing issues that come up and maintaining the equipment, the reliability engineer gets into:
- What’s going on with the equipment?
- How does it fail?
- Why does it fail?
- What can be done to prevent it from failing rather than fixing it when it fails?
Tim became the site leader for mechanical integrity and quality assurance. These are elements of process safety management within the OSHA 1910.119. By then he was leading a lot of the test and inspection programs and the inspection and quality control of incoming materials. In 1999, he became one of the first Six Sigma Black Belts at DuPont in the third training class. Tim completed his certification, working solely on reliability and maintenance related Six Sigma projects for about two and a half years.
He then went back to being the site reliability leader, where the role had expanded to having three more engineers and two more technicians. The group then had one leader, three engineers, and six technicians doing:
- Predictive preventive maintenance
- Reliability
- Managing the pressure vessel inspection program, and anything around maintenance and reliability technology support
Tim then expanded that site role to an unofficial business reliability leader role. He was leading multi-site problem-solving teams to address some of the common reliability issues across the plant.
In 2005, Tim left the plant to join DuPont’s corporate internal consulting group for maintenance and reliability engineering. He took over the responsibility of Root Cause Analysis across the whole company. He led the development of a best practice for writing maintenance plans and SAP. He also took on some of the ownership of DuPont’s internal version of reliability-centered maintenance.
Tim is now one of two subject matter experts in the company. He:
- Lead’s DuPont’s global reliability network
- Sits on the corporate strategic and tactical teams for reliability and maintenance
Which roles allowed him to better understand maintenance and reliability?
Tim uses the philosophy of ‘bloom wherever you’re planted.’ Every role he was allowed to take on was a chance to grow. It helped him better understand the craft he had chosen. Besides reliability and maintenance, he also got to learn about manufacturing and leadership. Every role has taught him aspects of:
- People
- Organizations
- Work processes
- Managing systems
- Equipment
- Chemical processes
- Packaging systems
- Tools and technology
In addition to DuPont’s internal work, Tim represented the company to other organizations. As a representative, he was able to gain an external perspective from other companies’ consultants, peers, and vendors involved in manufacturing. These opportunities gave him a broader view of what’s going on in the field, and to bring that back to DuPont. The experiences created value for him both personally and professionally. Always be open to learning. Listen twice as much as you’re speaking.
Which role got Tim to understand the people side of things?
Tim learned a lot as a first-line supervisor. The role helped him understand that even people from different backgrounds from his could still teach him a lot. And that if he treated them with respect, and acknowledged and valued what they knew, they willingly shared what they knew. That helped grow faster as a supervisor because he had a better understanding of what they did. Tim uses the principle that ‘All of us are smarter than any of us.’ So, in taking perspectives and learning from everyone around, you’ll come up with a better solution than what you would have come up with on your own.
Being a program leader also made Tim learn the importance of vision. He was the visionary for predictive maintenance in his plant and business. He saw what it could do and developed a passion for it, and people caught on to that enthusiasm for it. But he needed a plan to influence people and communicate what the value would be for them. He had to be able to show people where the priorities were.
Being a consultant also helps you understand people. You learn the importance of relationships and helping to solve the other person’s problem. By helping them, they’ll be more likely to embrace what you’re trying to do, making you more successful.
How did Tim decide if a new role was the right move for his career?
Tim’s a person of faith, so he relies on prayer to help him make a decision. He also uses the Bible which teaches that ‘Wisdom comes from a multitude of counselors.’ So, he would always talk to people he trusted to find out what they think of the role change. If you have wise counselors, you’re bound to get good guidance.
From a technical standpoint, every role change seemed like the next logical step in his career growth. And because he was giving results, the leadership allowed him the flexibility to do what he thought was the next logical thing to make it better.
The Six Sigma role as an outgrowth of all the tools Tim was already using as a reliability engineer. The return to a reliability leader role with a larger group was the next phase. Then taking everything he’d learned within the site and business, and making it available to DuPont was the next role. So, if you constantly look at how you can grow yourself and your impact, opportunities sort of present themselves.
What personal or professional development made the biggest difference in growth and understanding?
- The first would be transitioning from a focus on maintenance to a focus on reliability
- The second is predictive maintenance and FMEA based methods
- The third is performing Root Cause Analysis
What parts of maintenance and reliability are most interesting?
For Tim, that would be the technology end of things. The hardware and the methodology behind it are like RCM, like cause and effect mapping in Root Cause Analysis. He likes learning about:
- Equipment
- Components of equipment and maintenance practices like alignment and welding
- How equipment is combined in manufacturing systems to make products
Tim also likes to teach and share what he’s learned with others. And in turn, he also likes to learn from them. He likes bringing people together to solve problems. He likes facilitating methodologies and processes that cause people to leave knowing more than what they knew coming in.
What part is the most challenging?
Tim’s come to learn that the role of a reliability engineer is very much influential. The majority of leadership roles in the maintenance and reliability space are influence roles. That’s because the reliability engineer works with:
- Management
- Maintenance personnel
- Operators
- Production personnel
- Materials management people
- Project engineers
- Environmental health and safety people
- Sourcing
In the field, Tim realized the importance of looking for strategic partners. These are people you can help accomplish their objectives through the expertise, toolsets, work processes, and programs that you have to offer. So, if you can work together to solve your problem and their problem at the same time, you’re more likely to be successful.
What excites Tim most about upcoming advances in maintenance and reliability?
That would still be the technology. He sees predictive maintenance in a transition from walkaround, onsite programs, to online monitoring with remote analysis. There are maintenance workers and processes that have recorded the history of work done on a paper checklist. But things are moving to mobile technology and digitization. This allows companies to eliminate paper by electronically connecting to information needed in real-time.
There are wearable devices that maintenance and production people can wear in the plant now. These bring artificial intelligence, visualizations, and communication technology to the field. Thus, enabling them to connect with subject matter experts remotely who may be back in the plant, or in a sister plant in another part of the world.
There’s also technology that’s transitioning the role of the reliability engineer. In the past, you would spend about 80% of your time collecting data for analysis. You’d then reformat and prepare it for analysis. But today, using the available tools, data hierarchy, structures, and taxonomies needed, you can get data collection and preparation down to about 20% of your time. That way, 80% of your time goes to data analysis and corrective action.
What makes the biggest difference in being successful with the maintenance and reliability journey?
Be open to external ideas. Do not have a ‘not invented here’ mindset. Evolution is possible from within, but revolution takes an external perspective. So if you want to make a step-change in your performance, you have to have that outside perspective that doesn’t reject something because it came from somewhere else.
Final Words
In the maintenance and reliability world, the obsession that people have to financially justify every action, purchase, upgrade, or training class is unnecessary. It’s essential to give people time to apply what they’ve learned. The paybacks in the maintenance and reliability field are in the 10:15:1 range. Things are going to pay for themselves if you do them right.
Also, never stop learning. Spend some time each day on personal development. The highest value activities are things that leverage benefits in multiple areas at once. So if you can find something to work on today that will contribute to four of your six critical objectives for the year, that’s a high leverage activity. Focus on such things.
UE Systems has been the premiere source of ultrasound instruments, technology and support for 45 years. From handheld inspection tools, state of the art (& complimentary) software and now permanent sensors & 24/7 condition monitoring – UE Systems has everything you need to take your ultrasound program to the next level.
UE Systems also offers 5 unique online courses to further your knowledge and ultrasound program. These courses range from lubrication best practices to ultrasound inspection on mechanical, electrical, or steam systems. Learn more at https://www.uesystems.com/training/online-courses/
Eruditio Links:
Tim Holmes Links:
- Tim Holmes LinkedIn
- SMRP.org
- SMRP Annual Conference
- Air Disasters
- Chemical Safety Board’s Incident Investigation Videos
- Think Reliability Examples
- How It’s Made

- Social:
- Link:
- Embed:
Rooted In Reliability podcast is a proud member of Reliability.fm network. We encourage you to please rate and review this podcast on iTunes and Stitcher. It ensures the podcast stays relevant and is easy to find by like-minded professionals. It is only with your ratings and reviews that the Rooted In Reliability podcast can continue to grow. Thank you for providing the small but critical support for the Rooted In Reliability podcast!
Leave a Reply