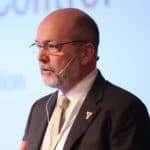
Learning from Failure with Jim Fitch
We’re excited to have Jim Fitch, the CEO of Noria Corporation and the director of ICML, back. He previously explored ICML 55, the standard around lubrication programs. ICML was founded about 18 years ago as a non-profit. It was to provide certification resources for organizations and individuals who needed certificates for completing their training. Noria Corporation is a for-profit services company that’s 22 years old. It provides training and consulting services globally, relating to oil analysis and lubrication. They also offer transformation services. These are for plants moving from their current state to something closer to the greatest reference state. Noria also publishes machine lubrication magazines among other e-publications. They’re also a conferencing company.
In this episode, we covered:
- What has Noria learned about failures related to lubrication?
- How many failures can be attributed to a lubrication-related issue?
- Do the employees’ skillsets and training levels contribute to failures?
- And much more!
What has Noria learned about failures related to lubrication?
Noria has conducted a lot of RCAs, or failure investigations. All the cases taken need to revolve around tribology, oil analysis, or lubrication. Half the cases are litigation or forensic related expert witnessing. The other half is that a machine or its component failed often, and efforts have been made to try to resolve it without success. You can sum it up by saying success is a teacher but failure is a better teacher. But you have to ask the right questions and be allowed to learn from the failure. Unfortunately, most organizations tend to be in the denial state. If something’s failed then it’s not their fault.
Lubrication and lubricants have a lot of information on the cause of a lot of failures. Lubricants are messengers of information to failures, where the root cause is independent of the lubricant. The issue could be a misalignment, overloading, defective design, and installation in an operator of what the root cause might be. So you go to the lubricant’s derivative to analyze what it has to tell you, determining the origin of the failure and its current state. That’s through analytical methods like analytical chemistry.
How many failures can be attributed to a lubrication-related issue?
Though many, there are failures that are a lot more prominent. Some of the most common causes of failures relate to:
- Ignorance
- Human error
- Human agency
The above causes can lead to errors such as:
- Using the wrong lubricant
- Mixing lubricants
- Using the wrong amount
- Wrong frequency of lubrication
- Uncontrolled exposures related to heat and decontamination
- Starvation
- Varnish and resin cases
- Moisture, corrosion, and microbial contamination
So, you take a failed machine, hoping the customer or client preserved the evidence well. From the evidence, a lot of questions get asked to collect discovery information. The discovery phase can be quite extensive. You have to go to the site and take sludge, deposits, or even varnish samples. These get sent to the lab to help start understanding what is going on. Samples can carry a lot of historical information. They could highlight things that happened before the failure, helping to come up with answers.
Do the employees’ skillsets and training levels contribute to failures?
Training on all levels is critical in helping to keep up with proactive maintenance. It’s easier to deal with things in a root cause state than in a failure state. If you educate your team on the virtues of contamination control, precision lubricants, and lubrication, and they have the skills, tools, motivation, budget, and support to do those things, you can avoid a lot of future issues.
What can organizations do to help investigate failures better?
Catching problems early is key. The beginning of the P-F interval is the root cause or proactive zone. You need to find out what the root causes are. You need to understand failure modes and rank them. This helps to develop a condition monitoring program around those failure modes, and the root causes associated with them.
The condition monitoring program should have the ability to catch incipient early-stage failure. This could be where debris seems to be at a very minor level, but it still shows up in the oil analysis report. You should also know how to recognize the cause of that. These issues never go away on their own. Instead, the move to a precipitous stage getting worse.
Also, know how to secure the crime scene. Don’t destroy, tamper with, or contaminate. If there’s an issue, you don’t want to mess up the quality of the information available. You need as many different pieces as possible to help create a picture of what caused the failure. Data, evidence collection, and fact-finding are all important parts of failure investigation.
What are organizations missing that could help prevent failures?
Modernized education for all your staff. A lot of people in lubrication use information they learned decades ago, rather than current information. There are better ways of doing things available now than in the past.
Ignorance and human agency are also worth looking into. Teach them what they should and shouldn’t do. have the organization in a proactive maintenance state. Understand what would-class lubrication means. For instance, ICML 55 is a standard developed by 45 renowned global experts. It’s a statement of what proactive maintenance is and what good lubrication prevents.
What can help mitigate lubrication related failures?
Instructors aim to teach things that work. Noria aims to teach competency in subjects they can bring back to their plant. It’s subjects that they can see a chance to take action on, with changes that result in benefits to them. To come up with these subjects, Noria looks at case histories. These are from its conferences and publications. In the process, they get feedback from the user community on what’s worked for them. And these are the topics you’ll find in their courses.
Contamination is one of the leading causes of failures. This occurs in different forms which can be noticed and measured through lubricant and oil inspection. Through side glass analysis, a lot of information can be collected. But a large percentage of oil and lubricant inspectors aren’t aware of this. For instance, Inspection 2.0 is a modern approach to gathering this information. Here, the inspector is actually an investigator. The investigator will investigate by taking samples, doing condition monitoring tests, among others. This helps them understand things from an earlier stage.
What to change when performing failure investigations?
You need to have the ability to tell when you’re in over your head. If a machine has suffered a major failure that you can’t deal with, be willing to seek help from other experts. By providing the information for others to help you, they will also reciprocate when the need arises. It’s impossible to know everything.
Words of wisdom
If you’re in the condition monitoring or troubleshooting world, you need an all-rounded education. You may have expertise in some areas, but you’ll need knowledge and information on peripheral subjects. You can go to conferences with speakers on different subjects. Buy books that relate to you doing your work well. Listen to podcasts and watch webinars. Get many certifications in peripheral and ancillary areas as well.
Machines have many causes and issues that need knowledgeable expertise. Users also need this knowledge because they’ll be performing proactive maintenance. Check industry standards, and use that to assess your organization, people, and levels of competency. It needs to give you a solution to the question of whether you understand what’s in that standard. Can you install different practices outlined within the standard? If not, you need to start learning how to get yourself from your current position, to where you ought to be.
Eruditio Links:
Jim Fitch Links:
- Jim Fitch LinkedIn
- ICML
- Noria.com
- Noria Facebook
- Noria Twitter
- Noria YouTube
- Machinerylubrication.com
- ICML55
- What is ICML55 with Jim Fitch
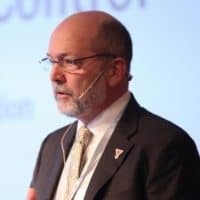
- Social:
- Link:
- Embed:
Rooted In Reliability podcast is a proud member of Reliability.fm network. We encourage you to please rate and review this podcast on iTunes and Stitcher. It ensures the podcast stays relevant and is easy to find by like-minded professionals. It is only with your ratings and reviews that the Rooted In Reliability podcast can continue to grow. Thank you for providing the small but critical support for the Rooted In Reliability podcast!
Leave a Reply