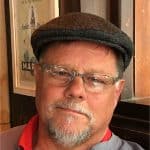
Defining Subsystems in an RCM Analysis with Doug Plucknette
We’re excited to be joined again by Doug Plucknette, an author, consultant, and instructor around maintenance and reliability, to talk about RCM analysis. This topic relates to a previous episode on failure curves.
In this episode, we covered:
- What is an RCM analysis?
- Why break down an asset into Subsystems to analyze
- How to break an asset down into Subsystems
- And much more!
What is an RCM analysis?
This is a way to develop a complete maintenance strategy for a process or piece of equipment and can be used on a single component. It looks at:
- How the component functions
- What can cause the function to fail
- What are the causes of those failure modes?
Failure modes are the reason why a component or part fails. Once you understand that, then you can go through a series of questions to focus on finding the correct tasks to eliminate, reduce the number of failures, or develop a condition-based task to detect that failure is occurring.
How to accomplish an RCM analysis
The key thing is to have a good team. Use people with some experience with the asset, whether it’s the design and installation for new things or something that’s been around for ten, twenty, or even thirty years. Then get a thorough understanding of the performance standards that the business expects from that piece of equipment. The performance standards are key in looking and getting a thorough understanding of how a process should work.
Ensuring that all the equipment associated with an asset is part of the RCM is a key part. Drawings are great, especially when you’re looking at new things again. For older equipment, drawings need to be up to date to represent what’s out there.
Why break down an asset into Subsystems to analyze
Subsystems are critical. If you don’t go out to have a look at the actual asset to find out its function, you can miss a lot. That, in turn, will lead you to miss key failure modes that will impact the performance of the piece of equipment or machine.
How to break an asset down into Subsystems
There are two ways to do that. The first is to start by looking at the main function you expect from the machine. You can do this by looking at:
- Electronic
- Mechanical
- Hydraulic
- Pneumatic
From there, you break the machine into those subsystems. The second way is to walk the asset down, breaking the different subsystems out. Functional block diagrams help a lot here if you’re a new facilitator who’s not familiar with the equipment or hasn’t done many RCMs.
Another thing that works is working with the team to draw boundaries of analysis. You can get sucked in to go way out into subsystems. You have to be able to say, “What are the boundaries of the RCM? What subsystems are included? How far back are you going to chase them?” Failure modes of the instrument on the machine will continue to happen. So, it would help if you had a recognition of where to stop and when to tell the team to go back.
How far do you need to break down the asset into Subsystems?
At the beginning of the analysis, you’ll talk about each component asset’s functionality. That then goes to the component level. When you get to failure mode level, you then get down to dealing with parts. Sometimes failure modes deal with components. They often deal with parts, and you need to talk about the failure modes of each.
Do you have to break down assets into Subsystems?
As you’re learning RCM, it’s important to do the detail of breaking that down. Create a hierarchy to get a map of what’s out there. Upload that into the RCM database to see whether what’s in your database matches your hierarchy. When you go to implement those things, it will be simple to know what should go where.
Having that type of discipline upfront helps in the long run to do RCMs the way they’re supposed to get done. And with experience, you’ll get to learn where the failure modes are.
How to figure out which Subsystems to use
The best teaching tool starts with understanding the ISO 14224 hierarchy and how it’s supposed to look. So, when you look at a particular machine, think of that hierarchy. Understanding the particular flow and how things are will prove a tremendous help in understanding what’s out there.
For new facilitators, you’ll be told, “We can’t give you our A1 machinist and A1 operator, so we’re going to give you this and that person since they’ve been here six months. They pretty much know the machine.” Getting good people will help the facilitator understand what’s out there and make sure they don’t miss. So more important than the hierarchy is setting up the correct team. Get people that know what’s out there to help you right from the start.
How do you approach this?
Experience is the key thing. To get that, you need patience. Don’t be afraid to make mistakes, and don’t be afraid to continue to ask questions. Continue to ask the right questions to become a better facilitator. It’s very rare for the team to lose patience with the questioning since you’re all there to learn. Ask questions like, “What can we do to eliminate the failure from happening again? And if we can’t, is it something that we can reduce the number of failures through PM or detect through on condition maintenance some way?” It’s a learning process, so don’t be afraid to ask the questions that will make you better.
Eruditio Links:
Doug Plucknette Links:
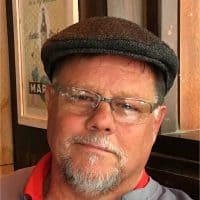
- Social:
- Link:
- Embed:
Rooted In Reliability podcast is a proud member of Reliability.fm network. We encourage you to please rate and review this podcast on iTunes and Stitcher. It ensures the podcast stays relevant and is easy to find by like-minded professionals. It is only with your ratings and reviews that the Rooted In Reliability podcast can continue to grow. Thank you for providing the small but critical support for the Rooted In Reliability podcast!
Leave a Reply