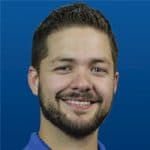
Why is it so hard to get Lubrication right with Bennett Fitch
Welcome Bennett who is the Director of Product Development at Noria Corporation.
Bennet has a background in Mechanical Engineering and worked in an oil analysis laboratory. Currently focuses on lubrication product development and has consulted for many plants enough to notice the common challenges
In this episode we covered:
- Why do organizations struggle with lubrication?
- What are the small things that make the biggest difference?
- How do we overcome current restrictions on training due to pandemic?
Why do organizations struggle with lubrication?
- Lubrication has an image problem; it is not exciting for teams.
- Technology has made significant progress in other maintenance reliability aspects but lubrication still lags behind.
Why don’t organizations focus on lubrication as part of maintenance reliability?
- What naturally excites people creates the culture; lubrication is inherently messy and isn’t exciting.
- Competing interests from other aspects of reliability where there are major technological advancements.
- Lubrication doesn’t occur intuitively to people
- Lubrication is considered an entry level task
- Lubrication is not well-trained even in graduate programs.
Management can drive the change by investing in; lubricant storage areas, storage conditions and training.
What are the small things that make the biggest difference?
They are not obvious threats but when seen it is often too late for equipment reliability. Training is essential to identifying the threats- this should be done in bits and frequently; not in large chunks at once.
Take for instance a contamination piece that cannot be seen by naked eyes pulverized to multiple pieces that can cause wear and eventual breakdown. Similarly, small incremental improvements in a lubrication program make the biggest difference in asset reliability.
Where do we start?
- Start with assessment of your plant to identify points that you can act on to make the biggest difference.
- Train on the value of a lubrication program to transfer knowledge and ensure collectivity.
- Use technological tools for the lubrication program to create interest.
How do we overcome current restrictions on training due to pandemic?
At Noria we have conducted multiple online training on machinery lubrication, oil analysis e.t.c.
Virtual trainings are better because;
- Technology has enabled training to be offered in smaller, digestible bits.
- We can include high level experts without a lot of difficulty.
However, it is challenging because not everyone prefers it.
How does culture fit into a lubrication program?
Culture is at the center of a successful lubrication program because when machines fail it is rarely because of lubricant designs, environment or operating parameters. The root cause is often human-induced.
Human factors include lack of protocol and mindsets to perform lubrication activities. People often say there isn’t enough time for lubrication activities.
All lubrication activities need to be matched to uptime and units delivered to communicate the value It creates and drive the positive culture.
What types of results should we expect from a holistic lubrication program?
- Huge savings on the lubricant costs
- Optimized labor due to higher equipment uptime
- Reduction on repair cost
- Less fault with asset vibration and thermography
- Good work environment that feeds into better culture.
How long does it take to put in place a lubrication program?
It depends on:
- Your goals
- The implementation plan
Note that it is continuous effort because of emerging areas of focus. However, typically it takes 1-3 years to cover all the aspects. The brunt of initiating the program takes 3-6 months.
Have a good implementation plan as a foundation. The exercise considers change management, accountability, and the program’s sustainability. It requires peer support more than a top-down directive.
What makes the biggest difference?
- Ownership of the lubrication program i.e. a champion who communicates, inspires others, listens and addresses the concerns from others.
Key takeaway
- Try to make the most difference where you can; be it lubricant storage, machine breathers, training or inspections,
- Presence of a lubrication champion who is the custodian of a lubrication program
Where can people find you?
- Webinars on lubepm.com
Favorite resources.
Machinerylube.com
Eruditio Links:
Bennett Fitch Links:
- Noria LinkedIn Page
- Noria.com
- Reliable Plant Conference
- Bennett Fitch LinkedIn
- ICML 55
- LubePM.com
- Machinery Lubrication.com
- Machinery Lubrication Reference Guide

- Social:
- Link:
- Embed:
Rooted In Reliability podcast is a proud member of Reliability.fm network. We encourage you to please rate and review this podcast on iTunes and Stitcher. It ensures the podcast stays relevant and is easy to find by like-minded professionals. It is only with your ratings and reviews that the Rooted In Reliability podcast can continue to grow. Thank you for providing the small but critical support for the Rooted In Reliability podcast!
On iTunes this episode is not available. It is actually a repeat of 260 – Practical Implementation of Technology with Simon Jagers when playing the audio.
Hi Harvey,
thanks for the heads up – I reset the feed and checked both on the show notes page and within iTunes and all seems in order now. Please give it another try.
cheers,
Fred