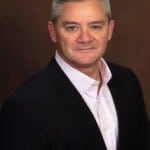
The Benefits of Processes with Scott Kelley
In this episode of the rooted in reliability podcast, Scott Kelley talks about the benefits of the processes. A process is a visual representation of work depicted in flow diagrams that demonstrate the path you have chosen along with alternative paths to accomplish your goals, also including the decision making.
A process gives you the insight into the most efficient methods of doing your work and then document them for future use. These processes are directly tied to policies and procedures of an organization. You can also use CMMS for gathering information and then implement these methods accordingly in a better way as you will know exactly what kind of system you need depending upon your requirements.There are following things that you need to know while building a process map; who does the work? Who authorizes the work? Who hands-off the work and who they hand out to? Who verifies the work? Who approves the changes? This part continues until all the stakeholders such as suppliers, owners, customers, community, employees, and regulators are involved.
Then comes ‘the what’ part. What is being done and what’s not? What is being added and what’s not? After that you have to know, when is the work being done? Does it occur on ad-hoc basis? Does it occur on rescheduling basis? It provides the movement and flow in the work. Next, comes where is the work being accomplished physically? Which building, cubicle, and floor? Then whether the work is regulatory? Is it critical? What triggers this type of work? How much work is needed and does it need authorization or not? All of these questions provide the criteria of the working environment of any organization. The processes cell also comprises of some facets that need to be taken care of.
- First, you have to identify your work. This work identification will also include the planning of your work, scheduling different tasks, and then coordinating them to different people. Then you have to know about the execution process of the work. There also needs to be some sort of auditory routine to determine the questions that need to be answered.
- Secondly, you will need a process for the requisition of the equipment. It will also include the purchasing of the spare parts, their maximum and minimum number limits and the approval methods for these spare parts. These methods can be implemented with direct or indirect approval. All of these are regulatory issues but they need to be done with a lit bit of understanding as well so that people can know about ‘the how’ part of these processes.
- The start-up of a process and then shut-down at the right moment also benefits the organization in the long run.
When you map out your processes, create them and then improve them, it means that your work is being done smoothly and consistently. The better execution of these processes results in greater productivity, reduction of operational expenses and risks involved, and ensuring safety with sustainable long-term management plans.
Eruditio Links:
- Eruditio, LLC
- A Smarter Way of Preventative Maintenance – Free eBook
- Maintenance Planning & Scheduling: Planning for Profitability Video Course
- Plant Hexcellence Article on Processes
Geometric Reliability Links:
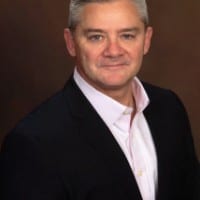
- Social:
- Link:
- Embed:
Rooted In Reliability podcast is a proud member of Reliability.fm network. We encourage you to please rate and review this podcast on iTunes and Stitcher. It ensures the podcast stays relevant and is easy to find by like-minded professionals. It is only with your ratings and reviews that the Rooted In Reliability podcast can continue to grow. Thank you for providing the small but critical support for the Rooted In Reliability podcast!
Leave a Reply