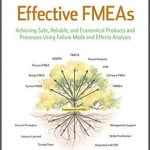
Making FMEAs Work with Fred Schenkelberg
In most of the organizations, Failure Modes and Effect Analysis, is taken as a light exercise where people come, argue, and leave without learning a single thing of value for their company. There is a lot going on when you are in need of FMEA because unless your equipment is failing, downtime is increasing, and you are losing big cash, why would you even bother to do FMEA right? Well, there is the answer why FMEA workshops lead to nothing knowledgeable in the organizations. FMEA is a very useful tool for you to know the causes of equipment failure and the steps you can take to prevent it from happening again.
For FMEA to be effective, you need to know a few things first. Why are you doing this? What kind of money you have for testing and analysis of different failure modes involved and what are you hoping to achieve from this process? For answers, you need to tie the FMEA with your asset criticality sheets, your machine failure data, and other information about possible failure modes. Then you need to start at system level FMEA and see if you find anything new. Otherwise just dig deeper to the component level and so on for gathering as much data as possible for analysis later on.
You have to know the failure modes first because that is where you actually know the causes of a failure. Then you would be able to set your priorities by creating a metrics. That will give your answers like; at what level is this going to affect us? How likely is it to occur again? And how can I detect and solve this problem? The most importantly, you need to highlight the biggest problems first and take corrective actions as you go about spending those limited resources that you will have.
You need to get the support of the whole team and management because they can give you the insight that you need to evaluate the choices and potential risks involved. Get your technicians and operations department committed because they are the ones who will benefit from this whole process. Having good facilitator makes the change management a little bit easier because the team listens to their honest opinions and trust the facilitator’s decisions if he can connect with them.
There might be some short-term mistakes and losses but all of it is for a larger gain for them. If it works out, it would make their routine work easier. That is why it is so vital to let them know the honest, hard work that is being done for them. The leader—the facilitator actually—should make people feel at ease as much as possible. Let them enjoy the training and study sessions because they would be more willing to perform the corrective actions they have been assigned and compete it while learning from it. The team should record, document, and discuss anything that helped stop or detect failures after analysis.
FMEA Links:
Eruditio Links:
- Eruditio, LLC
- A Smarter Way of Preventative Maintenance – Free eBook
- Maintenance Planning & Scheduling: Planning for Profitability Video Course
Fred Schenkelberg Links:
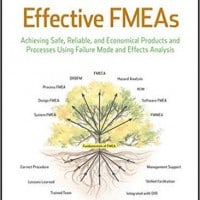
- Social:
- Link:
- Embed:
Rooted In Reliability podcast is a proud member of Reliability.fm network. We encourage you to please rate and review this podcast on iTunes and Stitcher. It ensures the podcast stays relevant and is easy to find by like-minded professionals. It is only with your ratings and reviews that the Rooted In Reliability podcast can continue to grow. Thank you for providing the small but critical support for the Rooted In Reliability podcast!
Leave a Reply