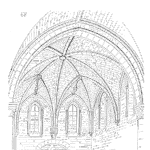
Creating Meaningful Reliability Predictions
Early and often during product development, the team needs to know the expected reliability performance of the current design. The values provide information to make decisions.
We have the ability to create meaningful estimates. Or, not.
The best time to estimate the reliability of a design is after all units have shipped and failed.
Thus we know when and why the units failed. This allows us to create an estimate that is fairly accurate. In practice we do not have this luxury, thus rely on a range of tools to create reliability predictions.
Let’s start with the notion that parts count predictions are pretty much fiction. They do not provide a meaningful estimate of field performance.
Using an industry database to find and tally failure rates is a futile exercise.
Engineering judgment, field data, vendor experimental evidence, physics of failure models, and accelerated life testing provide a range of tools that we can use to create an estimate that has value.
Sure, these approaches may take more work than a quick parts count prediction, yet provide meaningful results.
Over the course of a project, we may have the large uncertainty of only engineering judgment.
Later we refine the estimates using improved models and analysis. The intent is to provide feedback to the team in an ongoing manner to enable the team to meet or exceed the reliability requirements.
Let’s talk about what works and how to find the information you need to make reliability predictions.
Plus, we’ll bash Mil Hdbk 217 a little, too.
Providing estimates that forecast field reliability performance is our goal.
This Accendo Reliability webinar originally broadcast on 13 October 2015.
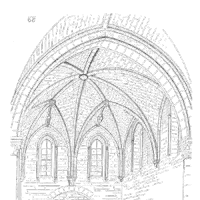
- Social:
- Link:
- Embed:
Please login with your site registration to view the video recording.
If you haven’t registered, it’s free and takes only a moment.
Leave a Reply