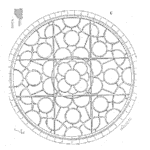
Life Cycle Cost Analysis for a Reliability Engineer
The investment in creating a reliable product pays dividends during the operation of the equipment or system.
The ability to estimate future savings or costs based on reliability engineering is key. Minimizing lifecycle cost occurs with reliability.
The concept of a product or system life cycle is not new.
We, as reliability engineers, encourage the investment early in the lifecycle for the eventual payoff (benefit) later during the lifecycle.
We employ design for reliability, robustness, and process control techniques, and many others, to ensure the system operates as reliably as possible. Yet, there is a cost to operate any complex system.
Maintenance, spares, and downtime to name a few. Early in the lifecycle just how do we estimate the benefits the suggested reliability improvement may create?
Let’s explore estimating the total lifecycle costs for a complex system from the point of view of a reliability engineer. Join me in a discussion on what to consider and how to estimate future costs while working early in the program.
You need to know this even if your system is not complex or repairable.
This Accendo Reliability webinar originally broadcast on 19 April 2016.
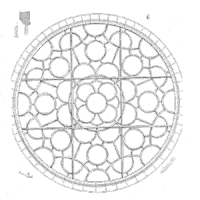
- Social:
- Link:
- Embed:
Please login with your site registration to view the video recording.
If you haven’t registered, it’s free and takes only a moment.
You may view an MP4 movie version of the event here (for non Flash playing devices)
[/show_to]
Life Cycle Cost (LCC) as defined in Air Force Manual (AFM) 800-11, is “the total cost of an item or system over its full life. It includes the cost of acquisition, ownership (operation, maintenance, support, etc.) and, where applicable, disposal.” Acquisition cost includes the cost of research, development, test and evaluation (RDT&E), production or procurement of the end item, and the initial investments required to establish an initial support capability (e.g., support equipment, initial spares, technical data, facilities, and training). More specifically, research and development costs are those costs associated with the research, development, test, and evaluation of system hardware and software. Included are the costs of feasibility studies; simulation and modeling; engineering design; development, fabrication, assembly, and test of prototype hardware and software; initial system evaluation; and associated documentation. Production costs are those costs associated with producing the end item, initial support equipment, training, technical and management data, initial spares and repair parts, plus other items required to introduce a new system into the inventory. Warranty cost is an acquisition cost that is included with the cost of production. Ownership cost includes the cost of operation, maintenance, and follow-on logistics support of the end item and its associated support system. The terms “ownership cost” and “operating and support (O&S)” are synonymous. Thus, the four major cost components of LCC are research, development, test, and evaluation; production; operating and support; and disposal. Therefore the model for LCC is: (LCC = RDT&E + Production + O&S + Disposal)