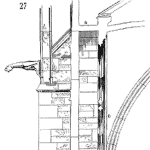
Best Practices When Dealing with Field Failures
Abstract
Kirk and Fred discussing the value of getting field failures returned for failure analysis and best practices in determining the causes.
Key Points
Join Kirk and Fred as they discuss the many SOR podcast and the questions we get back from our listeners
Topics include:
- The long life of electronics and an article that Kirk has written years ago that still gets a high number of reads, “Why the Drain in the Bathtub Curve Matters” (see show notes for the link)
- The critical value of getting failed products back and understanding the root cause of field failures. Low cost products that fail may be thrown in the trash as its not worth the customers time and money to return it.
- Field service engineers repairing capital equipment have a higher priority to get equipment repaired and back in production and may replace multiple parts leading to many good parts being returned.
- Many products that the reported field failure cannot be reproduced on the bench can be reproduced when environmental stress such as thermal or vibration is applied. Kirk discusses a actual successful example of this on field returns that seemed to be good.
Enjoy an episode of Speaking of Reliability. Where you can join friends as they discuss reliability topics. Join us as we discuss topics ranging from design for reliability techniques, to field data analysis approaches.
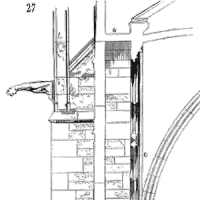
- Social:
- Link:
- Embed:
Show Notes
Click here for the link to the article by Kirk “Why the Drain in the Bathtub Curve Matters”
For more information on the newest discovery testing methodology here is a link to the book “Next Generation HALT and HASS: Robust design of Electronics and Systems” written by Kirk Gray and John Paschkewitz.
Leave a Reply