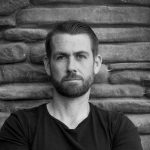
Setting Up to Report Monthly Failure Rates
Abstract
Chris and Fred discuss how we need to estimate monthly failure rates of a product. Like when bosses or directors want to know what the ‘failure’ or ‘return’ rate of a product is this month. But is this useful? How do we account for the number of products we have shipped? How old are the products when they fail? And how do we learn from these numbers? Can we even find a number? Listen to this podcast to learn more.
Key Points
Join Chris and Fred as they talk about monthly failure rates. So let’s say we get 20 returns in the first year of a product launch where we shipped 500 products. Is this good? What if we get another 20 failures in the second year where we ship another 1 000 products. So we now have a total of 40 failures over 1 500 products. Do we average these figures? Is there anything we can use these numbers for? The first thing you need to know is what you are trying to do or inform.
Topics include:
- You do need to know how much you are spending on returns this month. This is a simple accounting or business requirement. You need to know how much you are spending, are going to need to spend and so on. You can’t escape this.
- But if you want to know why your products are failing or if you will meet your warranty goals – you need to do more. And basic failure rates won’t help answer this question. You need to know other things like how old your products were when they failed. If your warranty period is based on usage – how many cycles had your products accumulated before they failed? It is all about the
- And another thing – returns versus units out this month doesn’t work. Let’s say this month you shipped 17 000 products this month – which is twice as many products you have shipped for any other months. If you simply divide the number of returns by the number of products shipped … then you will have a fantastic failure rate for this month. This is because all the failures are from previous shipments. And you are comparing this figure to a massive increase in units shipped out this month. This might give you a great failure rate metric for this month – but it is a mirage. It tells you nothing about the life of your product.
- And you need to know why things are failing. Particularly if you have dead on arrival (DOA) or infant mortality failures. Because these are failures you can do something with. You can look at your manufacturing processes or packaging for transportation. Is it a single batch (for example)?
- So how long will it take you to see something going wrong? Think about it. If there is an issue with your products. How long will it take for your failure rate metric to identify a problem? Will this signal be potentially hidden by bad metrics? … where simply increasing the volume of shipments means you see no problem? How much will this cost you when it does become an issue?
Enjoy an episode of Speaking of Reliability. Where you can join friends as they discuss reliability topics. Join us as we discuss topics ranging from design for reliability techniques to field data analysis approaches.
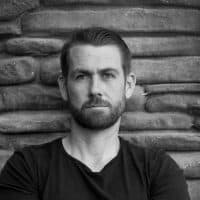
- Social:
- Link:
- Embed:
Show Notes
Leave a Reply