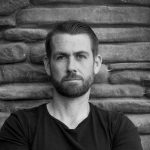
When and Why Around Assumptions
Abstract
Chris and Fred discuss assumptions – and when you need to check if they are valid. And if you do need to … how do you check these assumptions? Reliability (and all sorts of other engineers) need to study variation and variance. We are often interested in when the first ‘5 percent’ of things will fail. So assumptions on the underlying failure (or random) process are crucial. Sound familiar? Listen to this podcast to learn more.
Key Points
Join Chris and Fred as they discuss the many assumptions that reliability engineers are faced with throughout their roles. And these assumptions often revolve around capturing the random nature of a process. Like failure. And this is really crucial because reliability engineers need to know all sorts of metrics and values that are based on the nature of the random process. Things like warranty reliability, mission reliability, and service life reliability are all typically the point by which only a small number of our products or systems have failed. Which is not the average time to failure. So what do you do?
Topics include:
- Software will always give you ‘a number.’ And that number will always be ‘right.’ As in, it will process the data you input into the software and subject it to the algorithm or analysis you select. Which is often the ‘default’ one. Do you know what your software is doing to give you your number?
- Too many people are (1) unaware of their assumptions or (2) ‘hand wave’ until it is OK. Understanding the underlying assumptions is at best a dying art.
- It all comes back to the question you are trying to answer. If you can really define the question well, then the answer to your many questions about assumptions often become really easy to answer. All because you brought your analysis back to the reason you are doing testing or analysis in the first place.
- And sometimes – challenging and correcting your assumptions can be really good for you! In our recent webinar on probability plotting we showed how making an assumption created an upper confidence bound on failure probability of around 90 percent. But – when we removed an incorrect assumption the upper confidence bound on failure probability dropped to 10 percent. That error is huge! And you could have blown out an entire production timeline by simply making an incorrect assumption.
- And you really need to know what the central limit theorem is all about. This simply means that when we add a lot of random variables together, we end up with our stereotypical bell curve. And what this means is that when we have lots of data points our understanding of our ‘confidence’ in key metrics becomes really easy to characterize. But using the central limit theorem is of itself … an assumption! So you need to know when it applies.
- But assumptions don’t just apply to analysis – they apply to activities. How much will a failure mode and effect analysis (FMEA) save your organization? Well, this saving is based on the number of design and manufacturing deficiencies your FMEA team identifies. And also based on how much it costs you if you don’t find out about these deficiencies until ‘late’ in the production process. Can you know this before you do your FMEA? Of course not. But can you make some basic assumptions about how many critical deficiencies you will find and how much their prevention will save? Absolutely. In fact, you can’t do anything in life without some basic assumptions about the likely benefit of that activity.
Enjoy an episode of Speaking of Reliability. Where you can join friends as they discuss reliability topics. Join us as we discuss topics ranging from design for reliability techniques to field data analysis approaches.
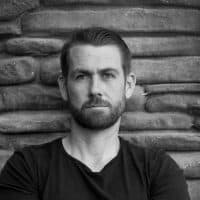
- Social:
- Link:
- Embed:
Show Notes
Leave a Reply