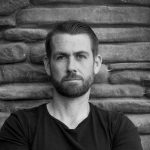
Wright’s Law and Reliability
Abstract
Chris and Fred discuss this thing called ‘Wright’s Law’ which is a really fascinating way of describing how things improve as we create more of them. And why is this relevant for reliability engineering? Does ‘reliability growth’ ring a bell?
Key Points
Join Chris and Fred as they discuss Wright’s Law, and how it relates to ongoing improvement in reliability.
Topics include:
- What is Wright’s Law? Wright’s Law states that every time you double the number of items you produce or manufacture, the cost per unit item decreases by 15 %. Why is this? There are a number of things. First and foremost – we learn as we go. So the mistakes we made for the first few products aren’t repeated later on. But then of course there are things like economy of scale, efficiencies, and so on. But a good chunk of this improvement (which we tend to see over and over again) is down to learning. Wright’s Law is a form of a power law that we see in lots of different applications across the world.
- So how is this relevant for reliability? Well … much of the costs and delays we incur in production are reliability-related. If a component prototype can’t integrate with the rest of the product, then that incurs costs and delays. It also represents an interface function failure which things like FMEAs are wonderful at preventing.
- … and reliability growth? Well … we know that traditional reliability growth (where we build-test-fix) sees reliability grow … using a power law very similar to Wright’s law. In fact, this thing called Duane’s failure pattern is a power law with this thing called a ‘reliability growth rate.’ Lots of studies and observations have found that this reliability growth rate is around 0.3 to 0.4. And what does that mean? Well … every time we double the amount of reliability growth testing, we decrease failure rate by 21.5 %. This is pretty close to 15 %!
- Are there any key takeaways? YES! Improving reliability through exploratory testing, learning from mistakes, and build-test-fixing is EXPENSIVE. So instead use tools like a Failure Mode and Effect Analysis (FMEA) to prevent as many problems as possible as part of your first design. For example, if we need to remove a certain number of defects and problems from our initial ‘raw’ design, you could halve your development time by eliminating 20 % of problems before you start. So why wouldn’t you? Why wouldn’t you take as many issues out of production as possible to do things like … incorporate design characteristics.
Enjoy an episode of Speaking of Reliability. Where you can join friends as they discuss reliability topics. Join us as we discuss topics ranging from design for reliability techniques to field data analysis approaches.
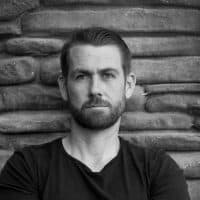
- Social:
- Link:
- Embed:
Show Notes
Leave a Reply