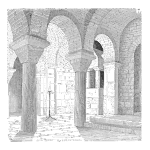
The practice of maintenance has been developing for the past 300 years. Since the start of the Industrial Revolution machinery and their control systems have played a critical part in our ability to produce consumer and industrial goods. Over that time different maintenance philosophies have developed in response to changing technology and increasing costs.
The progression in philosophies started with breakdown maintenance (BM), then to time-based maintenance such as preventative maintenance (PM) and shutdown maintenance. More recently condition-based maintenance (CM) has become significant. The next step is predictive maintenance.
Predictive maintenance (PdM) is closely related to condition monitoring since it uses the same investigative tools. But the difference is in the approach to using the tools. As the name implies we want to forecast or predict ahead of time when we must intervene and repair a piece of equipment prior to a significant failure. The aim is to use equipment-monitoring technologies to trend equipment condition and use that information to run the equipment differently and to decide if and when we need to fix it.
PdM is a technique that assists both operators and maintainers. Take an example of a large centrifugal pump set. Let’s mount some monitoring equipment on it. On the motor, we will put current draw detection with the readings reflected on the operator’s control screen. With this, we can track motor loads and see how hard the pump is working. We can detect if it is being over-stressed. It will also detect occurrences of deadhead and dry running.
The pump bearings will be fitted with vibration detectors and again the readings are put on the operator’s screen. This will let us check for an out of balance impeller, misaligned shafts (pipes move as daytime and operating temperatures change) and pump cavitation. Pressure transmitters on the pump suction and discharge complete the monitoring requirements. These too show up on the operator’s screen and tell us where the pump is operating on its curve and detect abnormal pressure conditions.
You can see that with all this information it will be easy to detect when the pump runs outside its designed operating envelope and do something about it before it is damaged.
So far we have spent between AUD$12,000 and AUD$25,000, depending on how sophisticated the current control system was. This sort of money can only be justified on truly critical plant equipment.
The challenge to people in maintenance and to plant and equipment designers is to fit low-cost monitoring equipment to as many items of the plant as possible. Clearly, there are big advantages to both the operator and the maintainer to be able to trend and predict plant and equipment condition and performance.
Mike Sondalini – Maintenance Engineer
We (Accendo Reliability) published this article with the kind permission of Feed Forward Publishing, a subsidiary of BIN95.com
Web: trade-school.education
E-mail: info@trade-school.education
If you found this interesting you may like the ebook Process Control Essentials.
Leave a Reply