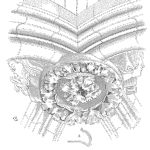
Preventative maintenance stops breakdowns. Preventative Maintenance requires people to regularly walk around looking, feeling, listening, smelling (sometimes even tasting) and thinking about their equipment’s operating condition. The three foundations of classical Preventative Maintenance are regular lubrication checks, drive train monitoring and equipment mounting inspections.
Keywords: work order, inspection, watchkeeping, CMMS, computerised maintenance management system.
Preventative maintenance (PM) work orders are easily generated by a CMMS and you should take advantage of this. PM’s require people to walk around looking, feeling, listening, smelling (sometimes even tasting) and thinking.
The three foundations of classical PM are regular lubrication checks, drive train monitoring and equipment mounting inspections. By establishing PM’s in just these areas there will be a noticeable drop in breakdowns within two months.
Lubrication PM’s should be raised to cover greasing and oil level checks. List the machine(s) to be greased and oiled and the gearbox oil levels to be checked. Tick check boxes as each machine is done. Use check boxes to tick if shaft seals are leaking. Don’t let seal leaks drain a gearbox of oil.
Make it clear where the grease nipples are so none are missed. Train the person doing the lube in basic lubrication theory. Tell them how vitally important it is to do the job well and to be continually on the lookout for lubrication and roller bearing problems.
Drive train monitoring involves inspecting vee-belts, pulleys, drive chains, sprockets and couplings for wear and over stress. Vee-belts are to have no cracks and a full profile without signs of wear. Pulley alignment is checked with a straight edge between pulleys. Pulleys should have no signs of slippage. Sprockets and chain links are checked for wear and alignment. Visually check the condition of coupling members transferring torque for signs of distortion and perishing. Where the same machine regularly shows up as defective investigate the cause and do an improvement project.
Equipment mounting inspections involve checking for loose mounting bolts and broken foundations, observing signs of
flexing base plates during operation, making sure pipe supports are taking the stress off connection points and feeling for unusual vibrations in the body of the machine.
The frequency of a PM is dependent on the industry, the site and the equipment. Lube PM’s are done more frequently than drive train PM’s which in turn are done more frequently than looseness check PM’s. However the periods can be adjusted with experience.
*CMMS –Computerised Maintenance Management System
Mike Sondalini – Maintenance Engineer
We (Accendo Reliability) published this article with the kind permission of Feed Forward Publishing, a subsidiary of BIN95.com
Web: trade-school.education
E-mail: info@trade-school.education
Leave a Reply