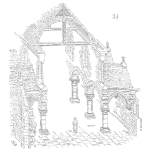
Preventive Maintenance or PM is a set of inspections and tasks that help prevent equipment from failing. Keeping equipment operating improves plant capacity and throughput. Avoiding unwanted downtime helps the plant avoid unnecessary expenses and lost productivity.
Checking the oil level in your car’s engine and adding more as needed, along with regular oil changes are examples of PMs.
PM Goals
PM work really has two primary goals:
1. Eliminate downtime due to maintenance-related failures.
This includes motor failure due to excessive vibration, low air pressure due to a faulty seal, excessive wear due to improper lubrication, etc. When equipment receives adequate attention from the maintenance team, it will fail less often.
2. Extend the operating life of the equipment.
A well-maintained piece of equipment may operate well past it’s expected retirement date. For example, keeping a motor well aligned, balanced, and lubricated will minimize the wear of the moving parts and place less strain on the electronic elements, thus forestalling premature failure or failures due to the loss of robustness.
Additional PM Goals
Another goal is the reduction of energy consumption. For example, an aligned motor doesn’t waste energy lost due to unnecessary friction. Cleaning air filters maintains the airflow with less blower work, is another example.
One other consideration is the safety and regulatory requirements for adequate PMs that both inspect and maintain the equipment.
Preventive maintenance is worth the investment. It is often difficult to see the benefits as the lack of downtime or failures minimizes the maintenance costs and when done well avoids the high profile failures and management attention to solve the problem though corrective maintenance.
PM Types of Activities
There are a few basic activities associated with preventive maintenance.
- Inspections
- Servicing
- Lubrication
- Fastening
Inspections look for damage, alignment, leaks, cracks, etc. All which indicate either an element of the equipment has failed or is about to fail. Some inspection may including measuring and monitoring wear or degradation of performance while still in the operating specification. The data enables the team to predict the appropriate time to repair, refurbish or replace the equipment.
Servicing may include alignment, cleaning, clearing or replacing filters, and verifying sensor operation. These are just a few examples and each piece of equipment may require one or more periodic PM tasks.
Lubrication includes topping off oils or other fluids and at times flushing and replacing the fluid. Advanced PM work may include analysis to determine the working condition of the equipment, nature of wear, or timing for lubrication change. The analysis may also detect contamination.
Fastening includes the initial equipment installation along with PM work to check the fastening system has maintained the equipment in its proper location and alignment. As elements are removed for inspection or replacement, the re-attachment must also meet the requirements of torque and equipment alignment.
Some studies show up to 50% of equipment failures originate from one of these activities. Performing these tasks well will minimize equipment failures due to faulty preventive maintenance activities.
Related:
Data to collect to optimize maintenance (article)
Fault Isolation (article)
Reliability Centered Maintenance (article)
I am very pleased to read this notes from Accendo. That’s so great!
Have a good view of preventive maintenance goals may help you be aware of many useful things. Besides eliminating the downtime, additional extra maintenance costs, employee’s injury or machine damage, you as well set out a proper preventive maintenance in the long run to improve the overall system efficiency and effectiveness. Do more to get more.
Think deep from now for your developing future!
Hi.
please I want to learn more about maintenance activities
thanks
Hi Adu,
You’re in the right place to learn more – be sure to check out articles under the on Maintenance Reliability category, https://lucas-accendo-site-speed.sprod01.rmkr.net/on-maintenance-reliability/
cheers,
Fred
I found it interesting when you described preventive maintenance and how it helps increase our machine’s lifespan. I bought a brand new car last month, and I’m eager to keep it in good shape, so I’ll follow your advice for sure. Thanks for explaining how preventive maintenance keeps a car’s motor balanced and repair-free.