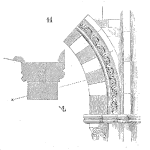
Continuing the series where we examine various roles within an organization and the ways in which each role interacts and affects product reliability, this post will start off with procurement engineers and managers. Since each role hereafter is a bit less involved, multiple roles will be grouped together. After procurement, we’ll take a look at warranty managers.
The role of a procurement engineer and manager
Procurement entails working with suppliers to obtain a supply of components or materials that meet the design requirements. The procurement team comprises engineers, managers, and support staff. One of its primary goals is to minimize cost. Often this means procuring the lowest price for a component that meets the design requirements.
The reliability role for procurement professionals is to obtain the best price for a component that meets or exceeds the reliability requirements. They should know the specific goal, including the probability of success, duration, local environment, and use, along with the design specifications. The conversations with suppliers should include conveying the reliability requirements along with learning about potential failure mechanisms.
Unfortunately, the focus on price often outweighs the perceived value of focusing on component reliability. Rather than building a working relationship with suppliers to quickly solve field issues, the focus should be on preventing design and component selection errors. Adding the cost of failure to the price equation often resets the procurement focus to include finding the most reliable components.
The role of a warranty manager
Products with warranties often include a warranty policy (terms and conditions of the offered warranty) plus some means to estimate future warranty costs and monitor warranty returns and payments.
The reliability role may include the following:
- creating and using accurate predictions of future failure rates,
- minimizing the costs of the reverse supply chain, and
- conducting failure analysis of returns and working to eliminate future failures.
A critical role is the feedback function that warranty tracking provides for the organization, as it represents the customer experience of the product’s reliability performance. Warranty acts as the scorecard.
Why is warranty so important?
Consider a medical device organization in which no one managed warranty. The Chief Financial Officer explained that warranty was not a major issue because it was an insignificant annual expense. However, about half of the products sold were returned within the warranty period. Although the manufacturing cost of each product was thousands of dollars, the cost of warranty was limited to the cost of the spare parts consumed during repair. Thus, senior management was unaware of the very large field failure rate. A warranty manager would have been responsibility for providing clear and appropriate measures of field performance. By increasing the warranty expense to include a call center, field service engineers, and the cost of replacement units, warranty for this organization would have accurately reflected the impact of such a high field failure rate.
Leave a Reply