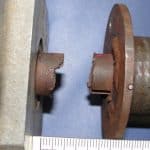
In a recent Accendo podcast, Chris Jackson and Fred Schenkelberg discussed who is responsible for producing a reliable product, which included designers and suppliers. I’m going to weigh in.
The reliability of any product depends on the reliability of the individual components and joints within the product. That is, the ability of the components and joints to withstand exposure to stressors without degrading to the point that they fail, resulting in the product no longer performing as required. Stressors, which include corrosion conditions, fatigue, and wear, were discussed in an earlier article.
Whether individual components and joints have the reliability required boils down to two basic aspects of engineering – selection and control. The appropriate form (i.e. shape, dimensions, features) and materials for components and joints must be selected during product design. Then, systems must be put in place to control fabrication of components and joints, ensuring their form and materials are as specified. This will enable the components and joints to consistently meet performance and reliability requirements.
So, who’s responsible for this selection and control?
Selection
Well, designers are responsible for selecting component and joint form and materials. They should understand the form and materials factors that influence how components and joints respond to the stressors and arrive at designs that enable meeting performance and reliability requirements.
So, designers need information about the stressors to which the components and joints will be exposed. Whoever is responsible for developing the product requirements is responsible for identifying the stressors and the expected life of the product. This might be the design team and/or marketing team. If it’s a contractor designing and making a component or sub-assembly for use in another company’s product – e.g. Tier1 for an OEM – then it’s the customer’s responsibility to provide the requirements. It’s also the responsibility of a contractor’s review team to verify a customer’s specifications are complete before bidding on the project – no one likes surprises.
Designers also need feedback about whether their designs can handle exposure to the stressors. So, reliability engineers must develop tests to evaluate component, joint, and product reliability. The tests usually involve accelerated conditions intended to cause failures in a short period of time. It’s important to develop acceptable accelerated tests and to perform them properly to get reliability data. Many products must pass a battery of verification tests, with the results fed back to designers if components fail during the testing.
In many cases, it is possible for materials engineers to conduct materials level reliability testing to evaluate the degradation behavior of different materials and component designs. The benefit of this approach is that information is provided to designers prior to performing verification tests, improving the likelihood of passing verification tests with fewer or no failures.
Control
Systems must be put in place to control component and joint fabrication so they, and the product, consistently meet performance and reliability requirements. This requires that the form and materials of components and joints be as specified. This control depends on people with different backgrounds.
First, there’s the designers, again. They must write a thorough list of form and materials specifications for each component and joint. Form specifications address shape, dimensions, features, appearance, and unallowable defects. Materials specifications include composition, the properties relevant to meeting a component or joint’s performance and reliability requirements, possibly microstructure, and types and amounts of materials defects. Designers should rely on materials engineers for help writing materials specifications.
Someone must also write specifications for bulk materials used to fabricate components and assemblies – stock metal, adhesive, solder paste. The specifications include composition, the properties relevant to meeting a component or joint’s performance and reliability requirements, properties relevant to how a material behaves during fabrication or assembly (e.g. metal elongation or solder paste thixotropy), possibly microstructure, and types and amounts of materials defects.
With good specifications in hand sourcing people and supplier quality engineers can identify suppliers capable of providing materials and components that consistently meet the specifications. It’s important to verify their technical capabilities, their understanding of the specifications, and their ability to consistently satisfy the specifications.
Materials engineers might also get involved during the supplier evaluation process, helping to evaluate stock materials and components from suppliers to verify their quality and reliability.
Manufacturers of materials and components have the responsibility of controlling their manufacturing processes. But if the people responsible for evaluating and selecting suppliers are on top of things, then systemic reliability issues will not originate with capable suppliers.
For companies with internal manufacturing capabilities, the production lines must have the systems in place to verify incoming materials, monitor and control production processes, and evaluate process output.
It’s not by chance
No one plans on designing and making a product knowing it’ll have poor reliability. But, many things must happen and many people must be involved to ensure good reliability. From my perspective, a big part of getting good reliability is selection and control of the materials used in a product’s components and joints.

Leave a Reply