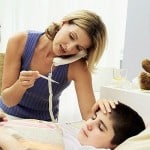
Engineers have been applying Prognostics to mechanical components for many years.
For example:
- Motors, increase in current or noise
- Mechanical pumps, progressive increase in vibration
- Thermal systems, time to achieve a set temperature
- Fluid systems, change in pressure
However, most industries building systems with mechanical components choose not to use prognostics because of the cost of the instrumentation within the product. Products that have on board “smarts” can choose to include diagnostics with less effort or expense. With advances in technology, the cost of the instrumentation is dropping. This not only means that adding the hardware to support advanced metrology is more feasible but that many of these components/systems may have already been added for other functionality and controls improvements in the product. It doesn’t take much brainstorming to find creative ways to use these existing sensory systems.
I worked with a team on a diagnostics program where we discovered we could use the microphone in the device to give an indication of the structural integrity of the plastic housing. Known sound levels would produce a different frequency (sound) profile dependant on how rigid the plastic housing components were fastened to each other. A progression in sound profile would indicate that the fasteners or heat stakes were loosening, a common wear issue. The product had a wifi connection, so a rigidity status/warning could be communicated to the manufacturer. A “preventative maintenance or replace” email could then be sent to the customer far in advance of any performance issues. It was a software update that added a prognostic function for an entire product line.
The biggest investment in creating a prognostic program is developing and implementing the “research” program that will profile these patterns of signals/indicators with system health. This can be a heavily iterative process.
The questions to be answered are…
- What failure modes are most common, we can’t monitor everything?
- What do failure modes of these systems look like as they progress from healthy to complete failure?
- What are the outputs we should monitor to identify the status of these performance factors?
- What existing monitoring on the system can be utilized and what opportunities are there for adding metrology?
Let’s not overlook the gems just beneath our feet! With or without a formal “test and analyze” program to study the correlation of signals, outputs, and health, we can mine our historical data and look for relationships. Some scrubbing of available data sets and a little statistical correlation analysis can yield some very interesting relationships between already measured signals and impending failure.
Only a few correlations need to be identified for further investigation to kick off a strong prognostics program, with justification for further funding.
-Adam
Adam has given a good introduction to Prognostics. Prognostic Health Management (PHM) is a methodology that permits the assessment of the reliability of a system under its actual application conditions, and exercises necessary management actions. To learn and apply PHM methodology, recommend joining the CALCE Prognostic and Health Management Group. http://www.prognostics.umd.edu/