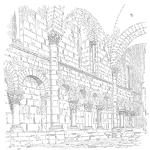
What readers will learn in this article.
- Bearings in dusty environments require added protection against dust ingress.
- The use of shaft seals and how they protect bearings.
- Eight dust ingress control methods for bearings.
- Good contamination reduction practices when assembling bearings
and parts.
Dusty surroundings are one of the most difficult environments for bearings.
In equipment handling powders or in processes generating dust the protection of bearings against contamination by fine particles requires special consideration.
Bearing housings
Bearings are contained within a housing from which a shaft extends.
The shaft entry into the housing offers an opportunity for dust (and moisture) to enter the bearing. The shaft seal performs sealing of the gap between the housing and shaft. Choice of the appropriate shaft seal and seal configurations to protect against dust ingress is critical.
Bearing housing seals for dusty environments may be either a labyrinth type or a rubbing seal type. The labyrinth type requires a straight shaft running true. Rubbing seals are the more common and allow for some flexing of the shaft. Figure No. 1 shows conceptual examples of each type of seal. When setting a lip seal into place to prevent dust ingress ensure the sealing lip faces outward.
In situations of high dust contamination, there may be a need to redesign the shaft seal arrangement for better dust protection than provided in standard housings.
Some ideas, which can reduce dust ingress into bearing housings, are to:
Figure No. 1. Shaft Bearing Housing Seals
i. provide two or more seals in parallel. Bearing housings can usually be purchased with combination seals as standard.
ii. retain the housing shaft seals but change from a greased bearing in the housing to one which is sealed and greased for life. If contamination were to get past the shaft seals, the bearing’s internal seals would protect it.
Figure No 2. Conceptual Sketches of Dust Sealing Methods
iii. stand the bearing off the equipment to create a gap between the end of the equipment and the bearing housing while sealing the shaft at the equipment.
iv. put in a felt seal wipe between the housing and the wall of the equipment to rub the shaft clean. Install of a mechanical seal in very harsh environments.
v. install a grease barrier chamber sandwiched between two seals. This barrier is separate to the bearing housing and acts as the primary seal for the bearing. Grease
vi. pumped into the chamber will flush out past the seals. vi. replace the grease barrier chamber instead with an air pressurized chamber.
vii. shield the bearing housing from dust with use of a fabricated rubber shroud encapsulating the housing and wiping the shaft or fit a rubber screen with a hole wiping the shaft over the opening emitting the dust.
viii. flush the bearing with grease by pumping excess grease into the housing and allowing the grease to be forced past the shaft seals or through a purposely drilled 15 mm hole in the housing. The hole must be on the opposite side of the bearing to the grease nipple, at the bottom of the bearing housing when in service and between the bearing and seal.
ix. Mechanical seals can be fitted to the shaft with the stationary seal sitting toward the machine and the rotating seal mounted back along the shaft. Combinations of other seals and wipers can also be used in combination with the mechanical seal.
(Some conceptual examples are shown in Figure No. 2.)
Assembly
The process of assembling a bearing into the housing must be spotlessly clean.
If contamination occurs at the time the housing is assembled no amount of external protection will stop the bearing from premature failure. When assembling bearings into housings make sure that:
- your hands have been washed.
- the workbench is clear and wiped down clean.
- no one creates dust or grinds nearby during assembly.
- fresh, clean grease is used to pack the housing.
- the components are clean and all old grease has been
thoroughly removed.
Breathers
When protecting bearings from dust you want to always consider another important area.
A breather is used to let hot air out of a confined space and then to let the air back in when it cools down. Enclosed bearings get hot when operating and cool down to ambient temperature when not in use. The air drawn back into the space needs to be clean of dust and moisture.
A breather on a bearing housing or bearing housing enclosure allows ingress of moisture and dust into the bearings causing premature life failure.
Often a breather is insufficient and should be replaced with a low micron air filter that removes dust particles two microns and greater in size.
Protect the breather or filter from water spray and damp conditions (ban hosing down if possible) with a shroud or by using an extension tube going into a clean, safe environment. Make sure the breather tube cannot be crushed closed by accident.
Mike Sondalini – Equipment Longevity Engineer
DISCLAIMER: Because the authors, publisher, and resellers do not know the context in which the information presented in the articles is to be used, they accept no responsibility for the consequences of using the information.
We (Accendo Reliability) published this article with the kind permission of Feed Forward Publishing, a subsidiary of BIN95.com
Web: trade-school.education
E-mail: info@trade-school.education
If you found this interesting you may like the ebook Bulk Materials Handling Introduction.
I think it’s so interesting that bearings need to be protected from dust. It makes sense, since such a small bump on an already small component could make a pretty big difference. I’ll be sure to keep this in mind if I ever get my workshop up and running! Thanks for the post.
Do PTFE bearings used in automotive linkages need to have dust protection? I was told by a distributer that the fact that they are PTFE means they need no maintenance and no dust boot.
What do you think ?