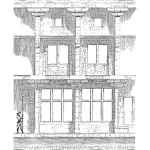
In this article on pulse jet bag house dust collectors we cover twelve factors spanning their design and operation.
A bag house dust collector is used to separate dust from a dust-contaminated gas stream. The gas is filtered through bags made of fabric. The fabric traps and filters out the dust while the cleaned gas passes through. The fabric consists of either woven or intertwined (felted) fibres. The bag fibre is selected for its ability to give a long working life within the internal environment of the dust collector.
Dust continually builds-up on the outside of the bags and a ‘filter cake’ develops. As the cake thickens the gas flow falls and less gas is filtered. To maintain the gas flow the dust cake is cleaned off the bag. The two common methods used to ‘drop’ the cake off the bags are to shock pulse the bag with an air blast or to shake the bag with a vibrating arm. Figure 1 shows a basic design of a pulse jet dust collector.
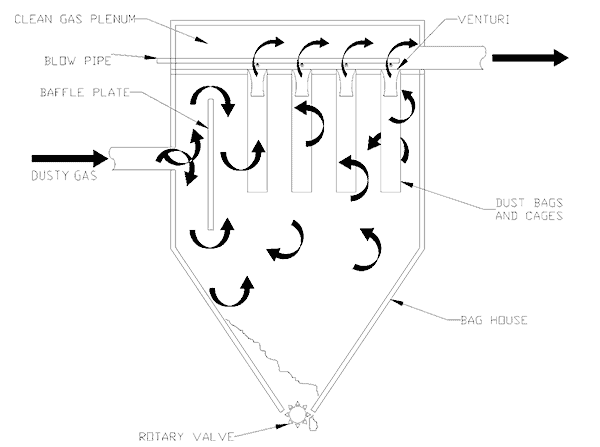
The dust bag is held open by an internal retainer or cage usually made of 3 or 4 mm wire. The retainer is slipped into the fabric bag after the bag has been dropped into place and the cuff in the collar at the top of the bag is sealed against the tube plate hole. A venturi is fitted to the top of the bag and helps the cuff make a good seal on the tube sheet.
The venturi creates a pressure shock wave when air is blown out the blow tube. A solenoid valve rapidly opens and closes blasting air out the blow tube holes. The shock wave moves down the inside of the bag, expanding the bag off the cage retainer and forcing the dust cake off the bag. Some designs of dust collector do not use a venturi but instead a nozzle is fitted to the blow tube.
From an operator’s perspective these items of plant usually require little attention. Provided process temperature, gas flow rate, gas moisture content, product acidity, dust loading and pulse air quality are suited to the fabric material, they ought operate for years with little down time except for an annual inspection and service of the pulse or shaker system.
Listed below are problems and solutions encountered with running pulse-jet bag house dust collectors. They represent the typical problems encountered by users of this equipment.
- Corrosion of bag cage retainer and venturi.
In high moisture-content drying processes galvanised or powder-coated mild steel bag retainers and venturi corrode quickly. When the cage starts to corrode the bag sticks to the cage. Up-grading to 316 stainless steel can greatly increase the time between cage failures.
- Bag fabric hydrolysis.
Hydrolysis is the gradual perishing of the fabric material through contact with warm dampness. It is a particular problem with polyester fibres. Change fabric type or change the process conditions.
3. Retaining cage fabrication quality.
Fabrication of the metal wire retainer cage must be to the highest quality. Poorly finished cages cut the bag fabric. Retainer frames must be smooth all over. All cut wire ends must be kept within the inside of the cage and welded end to end. All welds must be smooth and may require filing. No galvanising or paint dags are allowed as they will snag and rip the fabric. The cages must be straight and the collars square to the cage. They must always hang vertical with space around them and never touch neighbouring bags.
4. Clean top and underside of tube plate.
To get a good seal between the bag cuff and the tube plate both the top and the underside of the plate must be cleaned before fitting the bag.
5. Pulsing must be sharp and short.
The shock wave only occurs if there is a quick blast of air. The blow pipe solenoid must open & close in 0.02 seconds. Supply air pressure should be 650kPa.
6. Pulse air must be high quality.
The air used to clean the bags must be dry and oil free. You do not want moist or oily air on the inside of the bag. Install a refrigerated or desiccant air dryer and in- line air filter for the pulse air. Size the dryer & air filter for twice the airflow rate of the dust collector to allow for the surge flows.
7. Clamps on clamped bags are square to the cage.
If bag clamps are tipped to one side when tightened in place, it only takes a little shaking for the clamp to move and let the bag loosen. Clamps must be square to the bag axis so no space is left where the clamp can rock and slip off the bag.
8. Align blow tube discharge holes with axis of bag.
The air blast from the blow tube must travel down the axis of the bag. If the air blast hits the side of the bag or venturi it will wear away what it contacts.
9. Use removal tools that pull cages out square.
Unless the cage is rusted to the bag it can be taken out. It is necessary to lift the cage out square. Use tools that pull the cage out without destroying it or distorting the collar. Use a tight J-hook with a T-handle to slip into the bag and hook onto the retaining cage rings.
10. Once 10% of bags are blocked off change them all.
If a bag is holed plugging the top will seal it off. The bag plug must not leak. Closing off more that 10% of bags overloads the remaining bags and they fail faster.
11. Monitor the dust bag performance and fine tune.
Install a magnehelic pressure gauge or U-tube manometer across the tube sheet to monitor the dust build-up. The pressure difference across the bags will vary depending on the cake thickness. Bags need changing when the pressure difference across them reaches about 2kPa or 200 mm water gauge. Use the pressure differential to optimise the time between pulses and minimise mechanical damage of the bags.
12. Don’t walk on top of bag cuffs.
Once the bags are installed in the tube sheet do not walk on them as it may distort the cuff and not allow it to seal properly. Install two rows of bags along the edge of the collector first and then put their blow tubes back in. Plank over the blow tubes and work off the planks to install the next lot of bags. Continue planking over the installed bags and blow tubes.
Mike Sondalini – Maintenance Engineer
We (Accendo Reliability) published this article with the kind permission of Feed Forward Publishing, a subsidiary of BIN95.com
Web: trade-school.education
E-mail: info@trade-school.education
If you found this interesting you may like the ebook Process Control Essentials.
Mr.
I want to know the difference betewen a dust collector with enter air-solid in up part wit plate bafle and air-solid enter down.
What kind is better or more effiency?
I appreciate your comments
Best regards