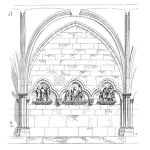
Often used to pump slurries, helical rotor pumps (also known as progressivity cavity pump, eccentric screw pump, mono pump) use a spiral rotor to move a chamber full of product through the pump. When moving slurries it is critical that the rotor wipes the rubber or elastomer stator firmly, else fine particles get between the rotor and stator and rip material out. This article discusses a major operating problem when the wrong size rotor was used in a stator.
Keywords: pumping abrasive, pumping slurry,progressive cavity pump, helical rotor pump, eccentric screw pump, mono pump
It’s been an absolute nightmare finding out what to do with a single stage progressive cavity pump that kept chopping out rotor and stator regularly for the past six months.
It was moving a 5%, 0.5 mm diameter sand slurry. No one knew what had changed. It had worked fine for 4 years during which time the rotor and stator was changed every 4 to 6 months. Then suddenly we were changing a rotor and stator every week or two.
What we found was that eight months earlier the supplier had recommended a change in rotor tolerance because of high process temperature. He suggested we try a thinner rotor to allow for expansion due to the temperature rise. We agreed to test it and in error the new item became the standard replacement part. New thinner rotors were brought to replenish stock.
The new rotor did not last long and a spare was installed. The spare was the thinner rotor. The rotor again did not last long and the spare was taken from store. It was a thin rotor. The spare was replenished but it was again with a thin rotor. These thin rotors kept being used at each repair.
This continued until production was severely affected. A thorough investigation highlighted the problem and it was corrected and previous bigger diameter rotors were put back into stock.
It should never have happened. The test rotor should never have become the standard replacement part. But it had and that error caused months of heart ache.
The entire experience brought a lot of learning to me about helical rotor pumps. I’ve summarised it all below.
- Have a very tight compression between the metal rotor and rubber stator so the rotor firmly wipes the stator and forces any fine abrasive along with the progressive cavity. We measured 0.8 mm difference in rotor diameter (nominally 50 mm diameter) between the thinnest and thickest rotor. The 80 C temperature rise would never have expanded the rotor to fill the gap created by using such a thin rotor within the stator.The pump supplier was concerned that with too much pressure between rotor and stator it was possible to rip the rubber out of the stator due to friction from the rotor. We have not experienced such failures in our processes, but I have no doubt that it can happen with certain products.
- The larger 0.4 mm gap between rotor and stator let the pump pressure recirculate and squeeze the particulate into the space between rotor and stator. The rising pressure through the pump pushes and deforms the rubber in the stator. The sand trapped against the upstream curves of the rotor rip across the deformed rubber stator as the rotor turns and both are scored.
- It is the compression between stator and rotor that seals the pump chambers.
- Skinny rotors are made by machining the rotor down from full size. The stator bore is left as moulded and is not altered after manufacture. To vary the clearance between stator and rotor you change the rotor diameter. As the clearance gets bigger, liquid under pressure will compress the stator elastomer and create a gap that allows recirculation within the pump. Flow rates will fall when reduced rotor diameters are used.Reduced diameter rotors would be useful when large, chunky solids, such as meat pieces or fruit, are pumped. But if you have solid particulate in the fluid then look into using a tighter fitting rotor.
- The straight line pump ‘curves’ published by eccentric screw pump manufacturers are the theoretic values for pumping water at 20o C against set back-pressures. They don’t normally tell you which rotor clearance was used in the test.In reality the service is not an ideal linear relationship between flow and rotor RPM. Rather the pump becomes more efficient at higher speeds and tends toward the ideal only at high RPM.At high pressure and low RPM’s the pressure squeezes the material in the stator and opens the gap between it and the rotor. Recirculation from the high pressure cavity to low pressure cavity then occurs. This is less noticeable at high speeds because the pressure surge does not traverse between cavities as quickly as the cavities progress.
- As the concentration of particulate rises use a lower rotor speed to decrease the wear rate. When abrasive particles are present consider using a bigger pump with a larger diameter stator and rotor and run the pump slower. This allows the same flow to be delivered at the same pressure but now the rotor surface speeds are much less and as a consequence wear is greatly reduced.
- To reduce the wear rate you can also reduce the local pressure at any point. To do this use a longer rotor and stator with an additional stage. As more stages are used to develop the same pressure, it allows the pressure to be distributed over a much greater surface area. This reduces local contact forces and the wear rate drops.
- Lubricate the rotor and stator with food grade grease when assembling the rotor into the stator. This will aid assembly and protect the pump from dry running on first start up.
You can get a great deal more information on solving helical rotor and screw pump problems in the Plant Maintenance Engineering PDF Handbook and the free helical rotor pump operation guidebook that goes with it now available at the Maintenance Management online store.
Disclaimer: Because the authors, publisher and resellers do not know the context in which the information presented in this article is to be used they accept no responsibility for the consequences of using the information contained or implied in any articles.
P.S. If you have maintenance engineering advice on industrial equipment maintenance, especially defect elimination and failure prevention of plant and equipment, or have made successful equipment reliability improvements, please feel free to send me your articles to post on this website. You can contact me by email at info@lifetime-reliability.com
Leave a Reply