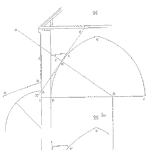
The short answer is, everything varies.
The longer answer involves the agreement between what is possible and what is desired.
If we could design a product and it could be replicated exactly, including every element of the product, we would not need tolerances. Any part would work with any assembly. We would simply specify the dimensions required.
Instead, variation happens.
Widths, lengths, weights, roughness, hardness, and any measure you deem worth specifying will vary from one part to the next. Manufacturing processes impart some amount of variation between each item produced. In many cases, the variation is acceptable for the intended function. In some cases, the vacation is unacceptably large and leads to failures. When the design does not account for the variation holes will not align, components will not fit, or performance will be poor.
When the designer understands the manufacturing process and naturally occurring variation, the design tolerances balance what is possible with what is necessary.
Functional System
The final product performance relies on each component functioning as expected. Gears mesh and wheels turn. The inputs to the system provide the desired output. Doors close securely, neither too tight, nor too loose.
Tolerances provide the range of values for each element of the design that permits the desired results to occur with each product produced. Instead of making the parts exactly to the drawing dimensions, if the manufacturer creates the item such that it is within the tolerances, the assembly will perform as the designer intended.
The customer reception of quality in part expects a good feel to a product. Meaning the components fit and work well together. Alignment, fit and finish are just right, and not noticeably off. You may have noticed the difference between poor and well-crafted dresser drawers. Poor drawers with poor alignment may bind when opening or closing. Whereas, well-crafted drawers work as expected without binding and do so smoothly.
Manufacturable
Tolerances stack up to the extent that a process done without care will cause parts to not fit at all or fit poorly, leading to failures and scrap. When parts do not fit, holes do not align, or connectors do not mate, the product is at a minimum not assembled correctly requiring repairs or is simply scrapped. Either way, the unnecessary costs mount.
The creation of individual parts, plus the variation of assembly processes, leads to the need for generous tolerances. Yet the design may require tight tolerances to function as intended. It is finding the balance between performance and the ability to assemble the system.
This is an economic balance.
It may cost more to maintain very tight tolerances. The cost of advanced manufacturing processes, or the cost of inspection and scrap, is balanced by the economic benefit of the customer perceived quality and willingness to purchase the product.
Cost of individual parts appropriate to requirements
There are many ways to form parts.
From cast to stamped, from die cut to hand cut, each process has inherent variability. When the process is stable and the equipment well maintained, the parts will reflect the inherent variability of the manufacturing process. Each type of manufacturing process has limits on precision and generally, the more precise methods are more expensive.
Using only very tight tolerance may require using expensive manufacturing processes of the parts. If not all part precision contributes to final performance then some if not most of the part tolerances may be less stringent.
This may allow less expensive part manufacturing methods and still create a product with the desired performance.
Dilemma of Communication About Tolerances
Design teams understand the need to include tolerances on part drawings and component purchase specifications. The designing engineers need to know the supplier’s capabilities to achieve specific tolerances.
Suppliers desire to create parts the meet the design requirements. Everyone is trying to do the best they can to together create a quality product.
And again, variation occurs.
Ideally..
Ideally, there would be no variation and the design nominal values would be sufficient. Variation adds complexity to the design.
Ideally, the design would accommodate the entire range of variation created with the parts. There would be no scrap or wasted material. Variation happens and designs that can accommodate the most variation are good (for the supplier).
Ideally, the part variation is stable and predictable and within the needs of the design. This doesn’t happen by chance. Communication between the design team and supplier has to be clear and complete concerning design requirements and part variation. The two sides have to find the happy balance that leads to an acceptable economic and quality solution.
Creating a product based on working with the part variation, permits a robust design to exist. A product that is economical to assemble, does not require rework or repair, and works as expected, is a great beginning to a reliable product.
This quick introduction to three statistical analysis methods enables you to quickly determine or assess part tolerances. Plus, you will learn why tolerances are critical to achieving a reliability product or system.
Please login with your site registration to immediately download this ebook which includes step by step examples and details on the data you need to get started today.
[popup type=”” link_text=”Login” link_class=”button”]
[/popup]If you haven’t registered, it’s free and takes only a moment.
Leave a Reply