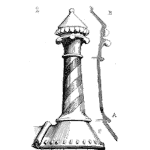
I like to say Reliability is all of quality over time. Quality professional tend to say reliability is an element of quality. David A. Garvin of the Harvard Business School suggests there are eight dimensions to quality, including reliability.
Either way one relates quality and reliability we need to remember that quality or reliability is not a department, team, the engineering down the hall. Quality and reliability is part of the culture of the organization. It is how we make decisions the impact how the product or service performs for customers.
The 8 Dimensions of Quality
According to Garvin, these are the 8 dimensions of quality:
- Per: Performance refers to a product’s primary operating characteristics. This dimension of quality involves measurable attributes; brands can usually be ranked objectively on individual aspects of performance.
- Features: Features are additional characteristics that enhance the appeal of the product or service to the user.
- Reliability: Reliability is the likelihood that a product will not fail within a specific time period. This is a key element for users who need the product to work without fail.
- Conformance: Conformance is the precision with which the product or service meets the specified standards.
- Durability: Durability measures the length of a product’s life. When the product can be repaired, estimating durability is more complicated. The item will be used until it is no longer economical to operate it. This happens when the repair rate and the associated costs increase significantly.
- Serviceability: Serviceability is the speed with which the product can be put into service when it breaks down, as well as the competence and the behavior of the serviceperson.
- Aesthetics: Aesthetics is the subjective dimension indicating the kind of response a user has to a product. It represents the individual’s personal preference.
- Perceived Quality: Perceived Quality is the quality attributed to a good or service based on indirect measures.
{Source: Eight dimensions of quality, Wikipedia article accessed 10 May 2018 at https://en.wikipedia.org/wiki/Eight_dimensions_of_quality]
For reliability professionals, we recognize the elements related to what we do, such as reliability, durability, and serviceability. Plus, we understand the need to create performance, features, and aesthetics that endure for some expected duration.
What is interesting is none of these elements are the purview of the Quality Department (some may argue that they do the conformance dimension, yet the quality folks are really just monitoring the work to others.) Organizations without an identifiable quality or reliability group still achieve some level for each of these dimensions. Some create remarkably good (high quality and reliability) across all these dimensions without attending quality or reliability engineers.
Since all these aspects of a product exist independent of a dedicated quality or reliability team, the decisions and supporting work occurs throughout the organization. Electrical engineers design for performance, yet also consider durability as well as all of the other quality dimensions. Industrial design engineers tend to focus on aesthetics, yet have to consider serviceability and conformance at a minimum in order to create a successful product.
In short, whether talking about quality or reliability we are not talking about the end of line measurements or accelerated life testing. We are talking about the many decisions that occur across the organization that result in the customer perceived attributes of the product’s behavior today and over time.
The Reliability Maturity Model
I’ve written about the reliability maturity model elsewhere, yet want to mention the concept here. The model is based on Phil Crosby’s work around the Quality Maturity Model in his book, Quality Is Free. In both, there are stages where the organization’s approach to quality or reliability is characterized as reactive, where the organization only responds to reported quality or reliability problems. Mature organizations are predictive, anticipating the potential problems before they occur.
The focus on the maturity models is on the culture around decision making related to quality and reliability. Are the tools, information, and behaviors in place which consistently result in the creation of a product that meets or exceeds customer expectations. The culture around decision making can be improved by the work of quality and reliability professionals, yet is typically not done by them. An organizations culture is more than one person or team.
Quality and Reliability Occur at the Point of Decision
The result of many individual decisions, from which component to use in this power supply, to the surface finish of the product case, and many more decisions, impact the ultimate quality and reliability of the product in the hands of a customer. Quality and Reliability rely on the culture of the organization to occur or are a result of the culture concerning decision making.
If your organization makes more decisions that improve the resulting quality and reliability then the resulting products perform and are perceived as performing well. If the decisions do not support creating a quality or reliable product then the results will reveal the impact of such a culture.
In either case, it is the moment of decision, the many decisions across the organization, that determine the results. Keeping this in mind as either a quality or reliability professional or even as someone wishing to create a successful product, may guide your work to create and support a proactive culture concerning making each decision.
Sir…. what should be ascertained first: validity or realiability of a tool ? Give reason of your answer ..sir plz explain this
Hi Stanley,
Let’s start with a few definitions. The validity of an item is typically accomplished in early customer testing (beta testing) or when customers are actually using the product. Validity is the process to determine if the designed item is meeting the business and customer needs that the item is supposed to accomplish. We use the term verification when checking if the item design and built meets the design specifications – this is often done during the development process and is an internal activity. Verification often is done with customers involved in some way.
Reliability is designed into a product, it is a characteristic of the item. We start checking or ascertaining or estimating an item’s reliability from early concept through till the end of life of the product line and sometimes beyond. We want to know the expected or actual reliability performance for many reasons – such as looking for unwanted or unexpected events, comparing to expected performance, or checking if the warranty accruals are adequate or not.
So to address your question, we should be checking the reliability nearly all the time and can check the validity when working with customers to set up requirements and again when customers have the item to see is it meets their performance expectations.
More directly we should understand how reliable an item should be according to the intended customers (validity), set the item’s set of engineering requirements, which includes a reliability target or goal, then validate that we have met the target, then validate with customers that we did indeed meet their expectations (verify)
cheers,
Fred
Dear Sir Fred
How should I cite this piece of work if used in my work and want to acknowledge.
Thanks
Also the on the reference list…
Hi CK, same as with citation answer, it really depends on the citation or reference list system you are using – cheers, Fred
Hi CK,
Thanks for asking and providing credit for the work. The citation details depend on the system you are using. For website pages or blog articles the formatting may be slightly different, yet the basic idea is to include the article title, author, url and date accessed (when you viewed the material)
cheers,
Fred