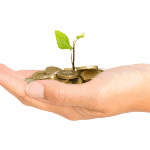
Being able to communicate the improvements with Maintenance Planning & Scheduling with finance and senior leaders can be difficult. The maintenance team sees a high PM Compliance, or more work being complete, but what does that mean for the business in tangible benefits? This is where the communication between maintenance and finance breakdown. By being able to identify and link the maintenance improvements to financial returns, maintenance will be able to generate support for current and future projects.
I remember trying to communicate with a finance person on how a CMMS would benefit the business. He could see how the CMMS would help with managing the system, but what financial benefits would the business see? I tried to explain the increase in wrench time, but he explained that the labour was a fixed cost. I explained how a high PM Compliance would increase uptime, but he wouldn’t believe it without data. Exactly what I wanted the CMMS for. My attempts were futile.
Over the years I have had the opportunity to further refine how I am able to link the improvements in Maintenance with Financial benefits for the business. Listed below are some of the quickest and easiest way to demonstrate the financial benefits often found in Maintenance Planning & Scheduling.
- Wrench Time Calculations
By calculating the improvements in wrench time, you are able to quickly and easily calculate a few financial improvements, such as reduction in Overtime, or the increase in efficiency of the maintenance department. So how is the improvements in wrench time calculated? By taking the baseline and comparing it to the improvement or estimated improvements. Once the difference has been determined, the return on the improvements can be calculated. For example, a small maintenance department with 10 craft people had a baseline of 30% wrench time. After maintenance planning & scheduling was introduced, the wrench time increased to 45%. Using these two numbers (45%/30%) you can see an increase of 150%. So what does this mean to the business? Quite a few things can be determined;
- Reduced Overtime
Reduction in overtime can be determined by trending the overtime numbers, or through the identification of improvements in the efficiency of the department. Using the example above, consider that each of the 10 craft people had an average hourly burden rate of $45 and work on average 2080 hours per year. At 30% wrench time, the craft was only providing value added work for 6240 (10 x 2080 x 0.30) hours out of a possible 20800 (10 2080). With an increase in wrench time to 45%, the craft provided value for 9360 (10 x 2080 x 0.45) hours.
If the department was running an average of 15% overtime, that would work out to 3120 hours per year (20800 x 15%). The increase of wrench time was able to ensure that the craft were able to provide an additional 3120 (9360-6240) of value added work, which cancels out all overtime. This would save the business approximately $210,000 per year in overtime wages.
- Increase in Efficiency
The increase in efficiency calculation can be used to demonstrate that the department was able to increase the amount of work it can complete, without adding any head count. This can be measured by determining the number of full time equivalents (FTE) that the improvements created, or by calculating the number of hours that the craft team is now providing value added work. Using the example above, the department of 10 people increased efficiency by 150%. Based on the hours saved (3120), the department is was able to achieve an increase of 1.5 (3120 /2080) FTE in the department, resulting in a savings of $140,400 (1.5 FTE x 2080 hours x $45). This savings can be realized year over year.
- PM Compliance = Increased Uptime
When calculating improvements in uptime or OEE it is a bit more difficult, as there are so many factors that can influence OEE / Uptime. It is best to trend the improvements in PM Compliance from the start of the Maintenance Planning & Scheduling program, and continue to do so on an ongoing basis. Once the PM Compliance baseline has been established, compare it to the OEE or Uptime trends. Now plot the trend together over time and see how much the improvements in PM compliance has impacted the OEE / Uptime. Excel has a great function (Correl) to determine if the increase in PM Compliance does in fact improve Uptime. Once this has been determined, you need to determine what each percent of PM Compliance is equal to in OEE or Uptime. This may require some detailed data analysis to determine. With the relationship determined, the savings to the business can be quantified. Typically each business knows what a percent of OEE or Uptime for a particular process or the site is worth in terms of lost opportunity costs. Using this number you would be able to determine the savings of benefits to the business. For example, a plant was able to determine that for each 5% increase in PM Compliance, OEE was improved by 1%. The lost opportunity cost for 1% OEE is $400 per hour. If the plant operates on a 24/7 basis, with a single two week shutdown, than a 1% increase in OEE would generate an additional revenue of $3,369,600 (24 hours x 351 days x $400).
In an instance where the PM Compliance rate is shown to decrease OEE or Uptime, than a Root Cause Analysis needs to be performed to determine why the PM Routines are not effective. This is where Fast Track RCM or Review RCM can be utilized to drive plant performance with effective PMs
Using either of these measures will enable you to determine Return on Investments for your maintenance improvements ahead of time, or to confirm your ROI estimates were correct. By using these you will be able to demonstrate the savings to Finance and senior managers, which should in turn enable you to drive further improvements in your operation.
What measures do you use to calculate the financial returns on your maintenance improvements?
Remember, to find success, you must first solve the problem, then achieve the implementation of the solution, and finally sustain winning results.
I’m James Kovacevic
HP RELIABILITY
Solve, Achieve, Sustain
Pictures of MoneyBy: Pictures of Money
No Fields Found.
I want to make sure that I get my home improved. It makes sense that I would want to plan for maintenance as well! That way I can ensure that my improvements stay working and functional.