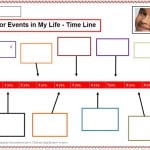
Definition of template
What is a template? Merriam-Webster has two definitions that seem to apply to RCA work. They are: 1) a gauge, pattern, or mold (such as a thin plate or board) used as a guide to the form of a piece being made; 2) something that establishes or serves as a pattern. For our discussion let’s use the second.
More, Better, Faster
In today’s work environment, everyone is trying to do more with less. If you have ever seen Billy Connolley’s Business Plan (follow the link for a laugh), you know what I’m talking about. Basically, tomorrow is not fast enough. This drives us to try to do “more, better, faster” in the words of some managers. I suppose we can’t argue with the concept of trying to do more, better, faster. I struggle with this when it drives people to cut corners due to self-imposed deadlines. I once told a boss of mine, If you can find someone who can write with both hands at the same time, please do because I can’t and will never be able to. I also told him that I can juggle three balls, but throw me a fourth, and I will drop them all. These comments are trying to convince you that while you can probably multitask, doing two things at once is very difficult. This leads us to try to speed up those things that we do touch, such as an RCA analysis.
Easier to modify than create
I’m sure most of you have heard the phrase “It is easier to modify content than create it.” If you are going to write a new work specification, don’t you go to the last one written, your template, that is close to what you want, and start from there? I did. All the standard language that doesn’t change was already in it, and all I had to do was modify some of the specifics for the new job. It took what would be a several day job and turned it into hours. I also need to make the choice and decide if there is no template close to what I need, it may indeed be faster and easier to start from scratch. This was even more important for us old guys, considering that I started doing this before computers. That is not a typo. We had administrative assistants who typed them and use mimeograph machines to copy them.
Templates?
It is natural to want to do this since we have already identified that there is time-savings to be had. It is only natural to want to use a template to allow you to be more productive and do “more, better, faster.” So, lets dig into an RCA template. It doesn’t really matter where you start, and to get your thought process going, let’s start with something you may normally not be working on. Let’s start with a broken leg. The beginning of the template might look something like this:
The first logical question would be “what caused the sufficient force applied?” I would hope that most would realize at this point that there are many ways to generate sufficient force to break a leg. For instance: slammed in a door, smashed into a car bumper while riding a bicycle (personal favorite), heavy object falling on it, jumping down from a higher place, another football player landing on it, hit by a pipe, hit with a maul, …… etc., you get the idea. I’ll even bet you were thinking about a “normal” leg. By that I mean someone with no known health issues. If you add that variability, you can move down the path of sufficient force and may have to add someone with brittle bones. This would lower the sufficient force criteria and open other possibilities.
Templates Factorial
I suspect that some may be thinking that I’ve started at the wrong place. The starting place is strictly up to the team or individual in charge, but I would say, that I definitely want to prevent a broken leg from happening again. Let’s start with one of the reasons for the sufficient force – say hit with a maul. Is there only one possibility? No. I can name a few situations, such as: swinging, missing the mark, and hitting your leg; someone else swinging, it glances off the intended mark, and hits your leg; an act of violence where someone aims, swings and hits your leg; it drops off a shelf and hits your leg. You get the picture. These scenarios all have different causal sets. We can continue the exercise with each scenario and realize that each cause has its own set of potential causes. My statistics are rusty, but I recognize that the number of possible charts is going up by factorial and gets big fast!
Equipment Templates
If you say “well, that applies to real life, but my situation is different, I am dealing with real equipment issues.” Let’s say you want to put a template together for an electric motor. Rather than expound on the causes of motor failure, I would refer you to an article I found titled “50 Failure Modes of Electric Motors”. As you can see, the problem is the same. With that many failure modes, the template gets big quickly to cover them all. We could, however, take the few most common failure modes and define a template around those. This can also cause some issues as common failure modes may vary between industries, corporate locations, environmental locations, etc. I did an RCA once where the group of process experts listed the ten ways a problem we were investigating could occur. We then put six of them on hold because the group felt they weren’t of any concern at the location we were at. We basically did the RCA on those four and developed the charts. From that, we started a template. The other six causes could be developed later and added to the template we started earlier.
Templates or Not?
Due to the above, I believe that there may be some common-cause paths that RCA practitioners may run into but, due to the extremely high number of variables and paths, it is just as easy to start from nothing. This doesn’t mean that you can’t keep past RCA’s and review for similarities. In fact, this should be done to identify common causes which will be discussed in another post. It also doesn’t mean that there aren’t some recurring themes, which there are. If you wish to document them and use them as templates, it might speed things up.
Lessons learned
Templates are a good thing, but for cause and effect analysis, they may not speed up the process
Templates might tend to lead someone down a path that was appropriate for one analysis but not for another
Certain causal paths do start popping up as you do more of these and can be considered small templates, but I prefer to call them common causal paths
Speed in doing RCA’s may be appropriate for items with low consequence, but trying to push speed over accuracy in a high consequence issue will not be valuable to anyone.

Leave a Reply