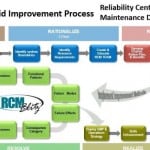
RCM Implementations don’t fail, believe me if you understand what your getting into upfront, use a proven process to select your asset for analysis AND you commit the resources, your implementation will be a huge success.
Looking back 20 years I can clearly remember performing my first RCM analysis and the ordeal that followed as we struggled to:
a) See the value in the analysis we had just completed (Someone told us that RCM should be performed on every piece of equipment at our plant so we selected one of our most common assets.
b) Free up the resources necessary to implement the tasks that came out of the analysis.
Lets be honest here, one of the biggest reasons why companies fail to implement is because we as consultants don’t give them clear detailed expectations on what the full RCM cycle is and in many cases when it becomes clear that Reliability Centered Maintenance is more than the analysis they have neither the time or resources necessary to implement.
This is something I think we all have struggled with at one time or another and if I understood what was really involved in completing a successful implementation I would have made darn sure we selected a winner and made very clear to my managers what the full RCM cycle really is.
1. Recognize – Select a critical asset that is suffering from equipment related operational, speed or quality losses
2. Rationalize – Baseline reliability data for this asset (How do you know if you improved if you never measured upfront?)
3. Ratify – Perform all necessary upfront work to ensure we have the right people identified and trained to perform the analysis and all the information the team will need to ensure a thorough and accurate analysis
4. Resolve – Perform the analysis and determine the mitigating taks
5. Realize the benefits by implementing and performing the mitigating tasks. Continue to measure and post reliability data, the progress of implementation and the savings that resulted from the analysis.
Think about it, the companies we work with on a day to day basis do all kinds of things that are more difficult than RCM. In fact the facilities their equipment resides in required a major amount of planning and resources to construct but before they started they had a plan and a budget.
I have yet to have someone call me to perform a RCM analysis on a plant that never got finished. Supply a good plan, communicate the potential benefits, resources and budget required to complete the project and we will have a winner. Last but not least, don’t start your second RCM until your first on is at least 80% implemented.
Leave a Reply