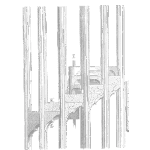
Abrasion is the removal of material from a surface by the movement of material across its surface. The factors affecting abrasive wear are the surface properties of the item being worn away, the abrasive properties of the material moving across the surface and the characteristics of motion.Where abrasive wear is a problem it becomes necessary to understand the mechanism of attrition. The following issues affecting the mechanism of abrasion need to be understood.
- The shape of the surface being worn away.
- The shape of the surface or particles doing the abrading.
- The hardness of surfaces and particles.
- The velocity (speed) involved.
- The momentum (a mass moving at a speed) involved.
- The contact time and contact angles during abrasion.
- Contact pressures during abrasion.
- Deformation characteristics of surfaces and particles.
- Chemical and physical properties of surfaces and particles.
- Properties of the components of the surface and particles.
- Particle size range.
- Moisture content effects.
If the product is in a slurry what is the effect on contact properties due to the presence of the liquid.
All and any of the factors listed play a part in the abrasion process. This provides many opportunities to alter the effect of abrasion by altering the influence of the factors.
Surface Properties
The most important characteristic for a surface to resist abrasion is its hardness. Second to that is its ability to resist surface yielding (indentation). Smooth, flat surfaces are preferred to rough surface finishes.
Hardness results are available for common engineering materials. The hardness test method needs to be appreciated to understand if the hardness being quoted is relevant to your situation. There are three common, but different hardness tests.
One lot are those that measure resistance to indentation such as Brinell and Vickers Hardness for metals and Shore Hardness for rubbers or plastics. Other hardness tests measure resistance to scratching (plastic deformation) by objects such as the Bierbaum and Moh tests. The third type of hardness test measures a surface’s ability to rebound or its resilience. Rockwell Harness is such a test.
Particle Properties
The behaviour of particles contacting the surface is as equally important in the abrasion process as the characteristics of the surface. The particles have properties such as harness, surface shape, impact behaviour, size and weight which affect the wear rate. It is useful to get a good appreciation of the characteristics of the particles. Laboratory tests are available but often it is sufficient to get a sample yourself and conduct your own tests.
These ‘homemade’ tests include:
- determining the density (weight per unit volume),
- looking at the particle’s shape under strong magnification,
- feeling (if safe to do so) the particles between your fingers,
- hitting a thin layer of the material with various solid objects (a hammer, piece of plastic, etc) on various surfaces and noting the remains of the particles and how they are imbedded in the surfaces under the sample and in the object,
- gluing some particles onto a wooden board with PVA glue, like making sand paper, and rub various materials across the abrasive surface to observe the effects,
- adding moisture to the particles and repeating the tests, • inventing your own tests to gain understanding.
Tests lead to a better understanding of what the surfaces and particles will do in the working environment and so permit you to make better material selection issues.
Motion Properties
How the surface and particles come together is important to understand. Are the particles being smashed into the surface or are they rolling across it? Are the particles being deflected as they move over the surface or are they moving straight over it? Are the particles heavy and moving at speed or heavy and moving slowly? Is the particle hard and sharp edged and likely to cut like a knife at high velocities? To be able to make a good material selection for abrasive conditions is well worth understanding the forces and motion that the particles will undergo.
The same abrasive material can have vastly different characteristics depending on the method of transport. For example lime paste slurry pumped through a pipe behaves very different to the same lime blown by pneumatic transport. The presence of the liquid in the slurry and the slower flow velocities reduces the wall friction. Whereas in pneumatic transport, particle velocities are much higher and surface impact forces are greater. A rubber liner in a lime slurry pump will last much longer than the same rubber lining in a pneumatic separating cyclone for lime.
Natural Rubber Linings
The performance of natural rubber lies in its unique properties of resistance, tear resistance, toughness and cross linking of the molecular structure. The rubber deforms under impact, absorbing the energy of motion at right angles with the surface and returning most of it to the particle as a rebound.
As a wear resistant lining care must be taken with regards the angle of impact, the particle size, shape and weight, the height of the fall and the velocity of impact.
The impact angle is of the greatest importance. At 90° impact angle resilience is the major factor in wear resistance. As the impact angle reduces tear resistance becomes more important. At low angles of impact specially fabricated surfaces are used.
In slurry service flat rubber sheeting is common.
Within certain limits, increasing particle size and height is handled by increasing the lining thickness. Tables are available for suppliers of lined equipment and pipes.
There is a critical speed above which natural rubber is unable to recover from wear and impact. At above 10 m/sec (3.25 ft/sec) the rubber cannot absorb the energy of motion and starts to fail.
Abrasion Resistant Coatings
Abrasion resistant coatings are typically smooth, having a homogenous (well mixed throughout), hard matrix loaded with small hard, round particles of various sizes. The smaller particles fill the gaps between the larger particles and support the larger particles when they take impact loads. The bonding agent must be a small proportion of the total volume, with the hard particle matrix making-up the vast proportion. The bonding agent is the weakest component and is protected from contact with the abrasive medium by being ‘hidden’ behind the exposed hard particles. Such a coating offers less resistance to the movement of particles across it.
Mike Sondalini – Maintenance Engineer
We (Accendo Reliability) published this article with the kind permission of Feed Forward Publishing, a subsidiary of BIN95.com
Web: trade-school.education
E-mail: info@trade-school.education
If you found this interesting you may like the ebook Bulk Materials Handling Introduction.
Leave a Reply