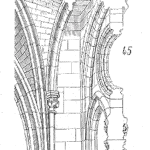
Worst-case tolerance analysis is the starting point when creating a tolerance specification.
It is a conservative approach as it only considers the maximum or minimum values of part variation—whichever leads to the worst situation. Setting tolerances such that the system will function given the expected variation of manufactured components improves that ability of the system to perform reliably.
In the worst-case method, you simply add the dimensions using the extreme values for those dimensions. Thus, if a part is specified at 25 ± 0.1 mm, then use either 25.1 or 24.9 mm, whichever leads to the most unfavorable situation.
The actual range of variation should be the measured values from a stable process. It may be based on vendor claims for process variation, industry standards, or engineering judgment.
Simple Example
Let’s consider a stack of five plates and we want to estimate the combined thickness. If each plate is 25 ± 0.1 mm, then the combined thickness will be 5 times 25 mm, for 125 mm for the nominal thickness. The math for the minimum and maximum is about as simple.
[NOTE: Checkout the ebook Statistical Tolerance Analysis]
The tolerance is ± 0.1 mm; thus, combining five plates at maximum and minimum tolerances provides a tolerance for five plates of ± 0.5 mm.
Thus, the stack of five plates will have a thickness of 125 ± 0.5 mm or a range in thickness from 124.5 to 125.5 mm.
Best Practices and Assumptions
Worst-case tolerance analysis is quick and easy.
You need just the tolerances of the components involved. There is no need for distributions or assumptions about distributions. We should have evidence that the part tolerances are real though. If the plate is specified as 25 ± 0.1 mm, then verify that the measured values actually fall within the range of the tolerance.
If the design function and the manufacturing process work using the worst-case tolerance analysis, then that is a safe way to set tolerances.
There are, however, cases where the tolerance stack is too large for the design or assembly process.
In that case, consider conducting the analysis using the root sum squared or Monte Carlo methods. The approach also works when considering the variability of loads or environmental stresses.
If you can handle the worst case, that may be good enough to create a reliable design.
This quick introduction to three statistical analysis methods enables you to quickly determine or assess part tolerances. Plus, you will learn why tolerances are critical to achieving a reliability product or system.
Please login with your site registration to immediately download this ebook which includes step by step examples and details on the data you need to get started today.
[popup type=”” link_text=”Login” link_class=”button”]
[/popup]If you haven’t registered, it’s free and takes only a moment.
Leave a Reply