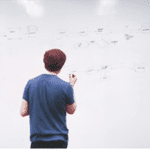
Selecting the Right CMMS can mean the Difference between Success and Failure
Imagine spending $100,000s or $1,000,000s on a software package that is supposed to improve your maintenance operation. A few years later you still have not seen any improvement and you did not generate any return on investment with the software. This happens every day when businesses select the wrong the CMMS.
Selecting a CMMS can be an overwhelming task, especially when so much rides upon the success of CMMS. You can read reviews and select a CMMS based on those, but the CMMS may not be the right one for you. The CMMS has to be fit for your business / operation or you will not see the right results. Thankfully there are two ways to select the right CMMS.
Use a Consultant
Most organizations do not want to use a consultant, as they feel they can determine the best CMMS themselves. This can be the case, if the organization has the resources and expertise to do so. In most cases the organization is lacking one of the two.
When you decide to use a consultant to select a CMMS, make sure they have experience selecting and implementing CMMS. Even if they will not be used to implement the CMMS. Most Maintenance and Reliability consultants provide this service, including High Performance Reliability.
There is also another option and that is a service like Software Advice. They use software professional to take your information such as you requirements and provide you with a short list of options with full reviews. This is a free service, and if you are interested, you can contact them here.
Use a Proven Method 5 Step Method
The other option is to use a proven method to select a CMMS. This type of approach ensures that all requirements are defined, and all factors are taken into consideration, resulting in the best possible solution for the business.
This method includes the following step;
- Needs Discovery: During this phase the needs of the business are determined and translated to what is required. The requirements should outline what specific features or functions the CMMS needs to have now and in the future. This may include having the software Cloud based, with a mobile option. Also it should include the specific functions of the CMMS, if customized reporting is needed, if integration to other software is required, the budget, and if implementation & training support is required.
- Determine Potential Vendors: Based on the requirements defined above, begin to determine a list of possible vendors that meet all the requirements outline.
- Narrow Down Potential Vendors: Using reviews, trials and user testing, begin to narrow down the list. You a quantitative ranking system to ensure the analysis is unbiased. Also be sure to look at company reputation and support. At the end of this step, the list of potential vendors should be down to 3 or 4.
- RFQ process: send out RFQs to the shortlist of 3-4 vendors. Be sure to include all requirements that the business requires now and in the future to ensure the vendor can meet those needs.
- Select the CMMS: Based on costs, functions and if it meets all the defined needs. It is important to remember that not all CMMS’ will have everything you need, so select the one that best fits your needs.
When you use inject rigor into the selection process and make it data driven, you are more likely to select the right CMMS. If you are looking to implement your first CMMS, or update your existing CMMS to a more modern version, you are now equipped with 3 options;
- Use High Performance Reliability Services
- Software Advice
- Use a Proven Method 5 Step Method
Remember, to find success, you must first solve the problem, then achieve the implementation of the solution, and finally sustain winning results.
I’m James Kovacevic
HP RELIABILITY
Solve, Achieve, Sustain
Follow @HPReliability
I like your advice on finding someone with proper experience to work on your software. This can have a huge impact on your business so be sure and do plenty of research. It can be the difference in how your company functions.