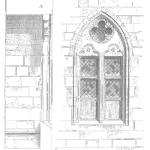
Roller bearing vibration measurement is one of the major condition monitoring tools in regular use. By measuring the velocity, acceleration and frequencies emitted from a rolling bearing it is possible to tell its condition and the likelihood of imminent failure. The technology is well established and well proven but requires a good understanding of equipment vibration characteristics before a user can draw good interpretations from the results.
Keywords: out of balance, vibration analysis, bearing life
Method of Bearing Vibration Monitoring
All bearings, even those in perfect condition, produce ‘noise’ as the elements roll over the raceways and rub against the internal cage and flanges. This noise is generated at high frequency and low amplitude. The bearing housing amplifies the noise to a point where a sensitive accelerometer can ‘hear’ them. By careful detection and filtering, the noise signal can be amplified and represented as a frequency series in real-time.
Most bearing faults occur with the rolling elements, cage or raceways. The frequency of the fault has a direct relationship with the geometry of the bearing and the relative speed of each individual raceway. Software libraries of noises for bearings in ideal condition are available for the vast number of bearings. By comparing the actual noise to the ideal bearing signature it is possible to highlight problems with the in-service bearing. The method of presenting the data is either by visually representing it on an oscilloscope screen (monitor screen) as waves or as a number on a digital display.
The Four Stages of Bearing Failure
A roller bearing progresses through four stages to failure. Vibration analysis permits the monitoring of the bearing’s progression through each stage and to estimate when failure will actually occur. In the case of a raceway failure, these would be the four progressive stages.
- The bearing is new and has no defects. This is the time to record its frequency ‘signature’ and normal operating acceleration and velocity values.
- If examined at this stage there would be no visible defects. However, under the surface of the raceway subsurface defects have started. The frequency signature has changed, the overall base level noise has risen and the velocity spectrum (graph) has risen higher.
- At this point the raceway shows visible signs of surface failure. The extent of the failure increases and grows with more metal coming off in minute sheets (delaminating). The velocity spectrum is much higher and much more background noise has developed. Within the background noise particular frequencies start to standout (side bands) and indicate failure is fast approaching.
- If the bearing is still in service everyone knows it is time to change it out because they can hear it. More vibration frequencies appear and more velocity side bands develop. Readings start to indicate amplitude changes and the noise moves into the range of human hearing.
A Great Range of Uses
Bearing vibration analysis can detect lubrication failures, misalignment, out of tolerance running, rubbing, improper gear teeth meshing, out of balance, bent shafts, loose components, worn parts, faulty couplings, improper operating conditions (like pump cavitation) and deflecting support structures. However to be able to analyse the presence of these type of problems requires a highly skilled person with much experience and exposure to bearing vibration signatures at various stages of failure.
Mike Sondalini – Equipment Longevity Engineer
Reference: Toward Plant and Equipment Reliability, P. Brown, Industrial Training Associates, (www.itatraining.com.au)
We (Accendo Reliability) published this article with the kind permission of Feed Forward Publishing, a subsidiary of BIN95.com
Web: trade-school.education
E-mail: info@trade-school.education
If you found this interesting you may like the ebook Process Control Essentials.
Leave a Reply