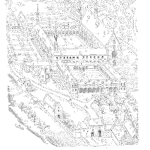
Two short questions to evaluate your knowledge of failure mechanisms (root causes) and common reliability models. The answers will be posted in a comment, later.
Which of the following failure root causes is most likely NOT due to power line variation (electronic-based product)?
A. Circuit design margin exceeded
B. Power dissipation
C. In-rush current response
D. Mechanical fatigue
Which theory is customarily used to calculate the effects of temperature on the life of a part?
A. Arrhenius model
B. Duane model
C. Miner’s rule
D. Inverse power rule
And, of course, each question could be reworded in a myriad of ways to explore many failure mechanisms, root causes, and reliability models. Part of the role of a reliability engineer is to have a solid working knowledge of failure mechanisms and how they commonly appear and are caused. Plus, we need a broad working knowledge of the range of models and approaches to understanding the effect of various stresses on failure mechanisms and life estimates.
Related:
Sources of Reliability Data (article)
Common Cause Failures (article)
5 books for a professional reliability engineer (article)
Answers and rationale:
Which of the following failure root causes is most likely NOT due to power line variation (electronic based product)?
A. Circuit design margin exceeded
A traditional failure mechanism due to power line variation
B. Power dissipation
A traditional failure mechanism due to power line variation
C. In-rush current response
A traditional failure mechanism due to power line variation
D. Mechanical fatigue
Correct – while power line fluctuations may cause mechanical and thermal variation within a product leading to mechanical fatigue, it is more likely due to cycling loads or thermal cycling.
Which theory is customarily used to calculate the effects of temperature on the life of a part?
A. Arrhenius model
Correct – especially for the change in chemical reaction rate due to temperature.
B. Duane model
Commonly used for modeling reliability growth rates
C. Miner’s rule
Commonly used to estimate the fatigue life of a part based upon applied stress cycles.
D. Inverse power rule
Commonly used for effects of voltage on dielectric breakdown (and other mechanisms, though not commonly used for thermal stresses.