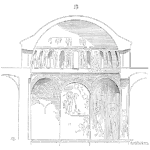
The root sum squared (RSS) method is a statistical tolerance analysis method.
In many cases, the actual individual part dimensions occur near the center of the tolerance range with very few parts with actual dimensions near the tolerance limits. This, of course, assumes the parts are mostly centered and within the tolerance range.
RSS assumes the normal distribution describes the variation of dimensions. The bell-shaped curve is symmetrical and fully described with two parameters, the mean, μ, and the standard deviation, σ.
The variances, not the standard deviations, are additive and provide an estimate of the combined part variation. The result of adding the means and taking the root sum square of the standard deviations provides an estimate of the normal distribution of the tolerance stack. The formula to combine standard deviations of the stack is
$$ \large\displaystyle {{\sigma }_{sys}}=\sqrt{\sum\nolimits_{i=1}^{n}{\sigma _{i}^{2}}}$$
Where σi is the standard deviation of the i’th part,
And, n is the number of parts in the stack,
And, σsys is the standard deviation of the stack.
[NOTE: Check out the ebook Statistical Tolerance Analysis]
The normal distribution has the property that approximately 68.2% of the values fall within one standard deviation of the mean. Likewise, 95.4% within 2 standard deviations and 99.7% within 3 standard deviations.
Simple example
Using the same example as with the worst case method, we have five plates which each will have different dimensions. For any given set of five, we do not know the five individual dimensions, yet we can estimate what those dimensions will be using statistics.
On average the plates are 25mm thick. And assuming each part will be slightly different than the average value and the normal distribution describes the variation, we then need to estimate the standard deviation of the part thickness.
For this example let’s measure 30 plates and calculate the standard deviation. If we find the standard deviation is 0.33mm we know that most parts will have dimensions within the tolerance of 0.99mm if the parts follow a normal distribution (more on how to check this assumption later). This is our estimate of how the part thickness actually varies.
Stacking five blocks, the average thickness is 5 times the mean thickness of 125mm.
We expect approximately 99.7% of the stacks of five blocks to have the combined thickness to be within the range of plus or minus 3 standard deviations of the combined plates. In order to combine them, we use the formula to add the variances and convert them back to a standard deviation with a square root.
In this case, we add the five variances, 0.332, and take the square root of that sum.
$$ \large\displaystyle {{\sigma }_{sys}}=\sqrt{\sum\nolimits_{i=1}^{5}{0.33_{i}^{2}}}=0.7379$$
And, since approximately 99.7% of the values are within +/- 3σ, the range of combined thickness values for the stack of five plates should be within 125mm +/- (3 x 0.7379mm or 2.2137mm) or most fall between 122.79mm and 127.21mm.
To estimate the number of assemblies outside the desired tolerance we can use the system normal distribution values, in this case, the mean, μ, is 125, and the standard deviation, σ, is 0.7379. Within Excell use the NORMDIST function. In general, construct the cell as follows:
=1-(NORMDIST(Mean+Tolerance, Mean, σsys)-0.5)*2
Where the mean is of the combined means of the parts involved in the stack. In this example the system mean is 125mm.
The tolerance is the desired value, in this example let’s assume we would like the total stack to be within 2mm of the mean, or tolerance of 2.
The σsys is the standard deviation of the combined parts found using the root sum squared standard deviations of the parts involved.
We subtract 0.5 to find the one-sided probability of the result being below the maximum value (mean plus tolerance), and multiple the resulting probability by 2 to find the chance the final assembly is either above or below the desired tolerance.
In this example, for a tolerance of 2mm, we would expect 99.33% of assemblies to have a thickness within the 125mm+/-2mm. This implies that we should expect one assembly out of about 300 to result in a thickness either thinner than 123mm or thicker than 127mm. By varying the tolerance in the calculation we can estimate the scrap or defect rate and compare the cost of scrap/failure to the cost of tighter individual part tolerances.
The accompanying spreadsheet provides this example worked out using the above approach. See the RSS sheet. tolerance analysis examples
Best practices and Assumptions
The normal distribution assumption relies on the process variation has many small perturbations that generally add to create the final dimension. It is best to actually measure approximately 30 samples to estimate the mean and standard deviation.
When gathering measurements is not feasible, then assuming the parts will have dimensions centered in the tolerance range and have plus or minus three standard deviations across the tolerance range is a conservative starting assumption. Of course, this implies the part creation process is capable of creating 99.7% of the parts within the tolerance specifications.
If measuring less than 30 parts to estimate the standard deviation, be sure to use the sample standard deviation formula.
$$ \large\displaystyle \sigma =\sqrt{\frac{\sum\nolimits_{i=1}^{N}{{{\left( {{x}_{i}}-\bar{x} \right)}^{2}}}}{N-1}}$$
Where N is the number of samples,
xi is the ith measurement,
And x̄ is the sample mean of the samples.
Related:
Worst Case Tolerance Analysis (article)
Variance (article)
Process Capability (article)
This quick introduction to three statistical analysis methods enables you to quickly determine or assess part tolerances. Plus, you will learn why tolerances are critical to achieving a reliability product or system.
Please login with your site registration to immediately download this ebook which includes step by step examples and details on the data you need to get started today.
[popup type=”” link_text=”Login” link_class=”button”]
[/popup]If you haven’t registered, it’s free and takes only a moment.
Hello, thanks for this article – it put some light on tolerances area I was not aware of.
Thanks once more,
Marek
Hi Marek, thanks for the comment. Now that you are a site member, check out the ebook on tolerance analysis. cheers, Fred
Brilliant article.
Only thing I am unsure about is the -0.5 for one sided probability. Perhaps you could shed some light ?
Other than that – very helpful
Thanks Matthew – and the -0.5 in the NORMDIST function is to strip out the other half of the probability, leaving only a one-sided result. I suppose it could be done other ways without the subtraction and multiply by 2, and would have to experiments and make sure the function rpovides the results we think it does. cheers, Fred
Doesn’t your formula answer the question how many assemblies are “within” the tolerance band? That is how I see it. I think the correct formula for your question should be 1 – (NORMDIST(Mean+Tolerance, Mean, σsys)-0.5)*2. Did I miss something?
hum, I think you are right… other thoughts?
Yeah, my other thought is I still learned a lot from your post. Thanks.
Hi Fred – was this updated on the toleranceanalysisexample1 spreadsheet?
Thanks!
AJ
no – I don’t thinks so… do not remember actually. cheers, Fred (will add to today’s list to check…)
Hello,
1. What is the use case of rss method?
2. what do you mean by tolerance?
3. When to use this method?
Sorry, I read the whole page but I still didn’t get good idea on it.
Hi Neil,
RSS and other tolerance analysis methods are used to set tolerances on design drawings. Tolerance is a range of acceptable dimensions or values for a component. For example, if a metal piece is nominally to have a width of 15 mm, we know that there will be some variation in the width of the actual manufactured pieces. RSS and other methods account for the amount of variation. The design then may include a tolerance for the width that may look like 15 mm +/1 2 mm.
When to use RSS, for any establishment of tolerances when you have data available on the variability of the specific dimension in question.
cheers,
Fred
Thanks for a good article.
You described the case of summation of two variables, X1+X2. How about X1*X2? Can we still use the same equation you mentioned to get the standard deviation of X1*X2? For example, one current source (+/- 5%) and one resistor (+/- 1%) would make one voltage reference. What’s the tolerance of this voltage reference?
Best Regards,
Hello Mr. Schenkelberg,
Thank you very much for this information. I am writing a paper right now and would like to cite this method. Do you have a published paper that I can cite? Thank you very much!
Best regards,
Payton.
Hi Payton, You can cite the article/blog post directly. My short article has not been published in a technical journal. thanks for reading… cheers, Fred
Mr. Schenkelberg-
While I have read this article and find it very interesting and informative, I have a question on calculating RSS. Can you have an infinite number of variables when calculating the RSS? I am assuming that you can, maybe I just need some reassuring.
Hi Jennifer,
Typically the RSS and other tolerance analysis calculations include only the elements that make up the item under consideration. The alignment of holes, the specific circuit voltage, etc. While some situations may have many elements to consider as each one has an impact on the resulting performance, they never have an infinite number of variables.
Besides, it would take an infinite amount of time to set up the calculation… right? And the result would be an infinitely wide range of variability.
cheers,
Fred
Hello,
really good article. I’m confused about one point – at the end you mention that without the oppurtunity to take measurements, use the sample standard deviation formula to estimate this.. but the formula includes xi which I think is the measurement… Confused how to get xi without measuring!
Hi Jonathan,
The idea when unable to make measurements is to assume both the mean and standard deviation – not to calculate them. The mean is assumed to be centered within the tolerance range and the standard deviation may be estimated by dividing the tolerance range by 6 (assuming 6 standard deviations – plus/minus 3 – just spans the range).
cheers,
Fred
Hello Mr. Schenkelberg,
I am an Electroemchanical student, i want to know how can i reference your article, it was recommended to me from my assessor for a spring project program, also its been really helpfull.
Regards
Depending on the system you are expected to use there is probably guidance on citing a blog or webpage – here’s is one way: https://libguides.nps.edu/citation/chicago-nb#website
cheers,
Fred
PS thanks for reading our work
Hello,
I have an RSS problem I am hoping to get some insight on. I am trying to use the RSS method to calculate the tolerance of lead in depth. I have never done an RSS analysis using an angle and/or trig.
I have the following varying dimensions:
Lead-In Diameter
Lead-In Angle
Bore Diameter at base of lead in
Hi Matthew,
Good question and one that I’m not sure if I have a good answer. My suggestion would be to focus on how each elements variation causes a difference in the resulting fit (length, width, or the dimension of concern) and proceed from there. For example, convert or transform the angle of attack variation into ‘width’ variation – or, I should say distribution, and proceed.
cheers,
Fred