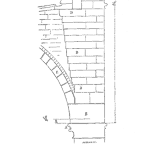
How operational loads break the drive shaft of a horizontal screw conveyor auger
Questions and queries asked following a screw feeder shaft breakage on a 15m long fertiliser dust transfer feed conveyor
If you have rotating shafts breaking at the drive-end of the auger shaft you may have a combination of bending and torsional fatigue. You are welcome to read the series of emails and responses below to a screw conveyor auger drive end failure.
Hi Mike! I would like to have a discussion on the failure of a screw conveyor at the drive end.
Industry: Fertiliser
Feed: Superphosphate dust
Tonnage; 37TPH
Failure: On screw auger pipe near the start flyte. Not weld failure but pipe sheared.
Failure has occurred more than once at start up.
Drive: Combination of belt and shaft mounted speed reducer.
Motor: 18.5 kW 4P 1450 rpm; Reduction ratio due to pulleys 2.366:1; Speed Reducer: 12.74:1; Has a variable speed drive (VSD); setting 44.2 Amps
Possibility: The system is likely to bog down due to blockage downstream, but the shaft broke when there was product in the trough and there was no blockage down stream.
I would like to establish what is the allowed torsion on the Screw Shaft of 5 inch, STD weight pipe. The length is 15 metre, there are 5 Cast Iron greased hanger bearings.
Hello Alan,
Glad to help where I can. Before we can do much I need to get a fuller understanding of the equipment design and its duty.
I need to see the P&ID and understand the logic to its operation.
Tell me more about the duty, such as running time, variations in the material flow rate through the conveyor (min/max/average operating transport rates), process control logic, how many stop-starts in a day/week, etc.
Do you have any photos, including design and assembly drawings of the installation that you can send to me. I would like to see engineering details on the feed into the trough, the discharge from the conveyor, the incline of the conveyor, the bearings and also get a general impression of the installation, such as where the motor is positioned, etc.
Do you have any specs on the dust and can you take a photo of the dust in the trough so I can appreciate its consistency and composition.
One final thing for the moment is to get a complete maintenance history of the equipment as far back as you can. Not just of the shaft but for the whole machine, including the drive gearbox, motor and the shaft bearings. If the shaft is failing it is likely that other parts of the machine, such as the drive end bearing and even the gearbox, are suffering and breaking often.
Equipment and its duty:
Equipment: Screw Conveyor, Approx 15 m long, Screw shaft 5 inch STD weight pipe, Dia of Screw 508mm, pitch 381. 5 CI Hanger Bearings
System: Feed end: Weigh Belt conveyor; Discharge end: Vertical Mixer. Connection between the Vertical Mixer and Screw Conveyor is a HDPE pipe with no break. If Vertical Mixer Bogs, the Screw Conveyor will start filling up. There are multiple stop and start.
Running time: 8 to 9 months of the year. When the plant is going, it is 24/7 operation.
Variations in the material flow rate: Two speed settings are used. 37 TPH and 60 TPH. The screw failed at 37 TPH setting at start up.
Process control logic: Do not know much at this stage. I was informed when I queried this that first the vertical mixer starts, receives solids from the Screw Conveyor, then liquid feed enters which starts the mixing in the vertical mixer. Downstream of the vertical mixer is a Kneader. The Kneader can block as well.
Stop/start: Prior to failure, allow 7 stop/start in a day.
Photos: See photos below
Feed into the trough:
Discharge from the conveyor: Shown in the photo.
Incline of the conveyor: Flat on the ground, inclination to horizontal: Zero.
Bearings: Intermediate Hanger, drive end Spherical Roller, discharge end Thrust bearing
General impression of the installation, such as where the motor is positioned, etc: As seen in photos.
My impression is that the screw conveyor is not designed for the duty.
18 kW 4P motor with VSD and speed reduction of 30 may be overkill. My thoughts are that 7.5 kW motor should be adequate.
The Screw Conveyor should be isolated from the vertical mixer with a clean break. The plastic tube should be replaced by a second screw conveyor receiving feed from the screw under scrutiny and supplying to the vertical mixer. If vertical mixer bogs, than the feed screw to the vertical mixer stops and the system stops.
Too many start and stop are causing fatigue of the screw.
Do you have any specs on the dust: No; Dust is free flowing, allow BD as 1520 kg/m3
Photo of the dust in the trough so I can appreciate its consistency and composition: Provided
Hi Alan,
I should have asked whether the dust builds up as a crust on the bottom of the trough, and to send me close-up photos of the break and photos of the break location along the shaft. (photo sent: Crust does build up)
When the shaft does bog, how is the problem tackled by the operations people? Do they try stop-start to break the friction and clear the bog?
The operator says that they hit the flight with a hammer. The flights have caked-up material on full flight in bogged condition.
You should also read the operation shift logs about the conveyor to learn what happens to it when it is in operation and how it is treated by the operators when it gives them trouble.
I will try to find out. Speaking to the Process Engineer, I am informed that even though the operator logs the stoppages, there is not enough information to understand what has been happening.
I forgot to mention in my earlier writing that there is a second feed in the mid-section of the screw conveyor.
Thanks Alan,
Lots of good information to help me understand the situation.
Please can you tell me where the breaks happen along the shaft. A photo or a manufacturing drawing with an arrow making the spot(s) would be great. If there is more than one location of breakage show them all.
How many times has a shaft broken before? Can you send me the dates that each breakage occurred?
What is done to address the failure; is the shaft repaired or replaced completely with a new one when it breaks?
When the shaft breaks how full is the trough?
What end is the drive at, discharge or infeed? (Pulling bulk material through a trough is much less troublesome and generates less forces on the shaft than pushing bulk material through the trough.)
Where the breaks happen along the shaft:
In the pipe immediately after the flange connecting the drive shaft to the auger but not at the flange weld. You can see where the pipe broke on the screw shaft near the flight. The maintenance team put a web to strengthen the pipe. Second time it broke downstream of that.
How many times has a shaft broken before? I am informed of at least two incidences in a year. The shaft was repaired and put back. I cannot give you dates.
When the shaft breaks how full is the trough? 35-40 percent
What end is the drive at, discharge or infeed? The feed end. The shaft always breaks at the feed end near the flange.
The shaft appears to be going through fair bit of variation in load. This could be due to two different feeds on the same screw at different locations at the same time.
See drive motor load current trends from fifteen minutes before the failure.
Dear Alan,
I don’t believe the motor size is the main problem. The motor will only develop torque in reaction to a load. The shaft is seeing a high load on a regular basis and the motor reacts to force the flights to turn against the load. I would first look at product build-up in the trough and understand how product can be jammed or build-back and prevent flow. It sounds like the discharge end can get full due to downstream problems then the dust backs-up into the chute but the conveyor keeps turning and driving regardless of the blockage. Can the build-back be controlled with program changes to match the flyte rotational speed to the demand from the mixing tank?
You can see from the motor current load graph before the shaft failure that the motor is not overloaded at first. Then something happens to it to rapidly raise the load 20 percent and a few minutes later something more happens to raise the load another 20 percent and cause the shaft to fail. You need to know what caused those step changes. If I were you I would run some trials with Operations and mimic the load changes to understand what causes them. You might find an easy answer to the problem once you know what caused those step-changes in the torque.
Since the side stream chute feeds into the trough at the same time as the main feed there is bound to be additional load on the shaft Is this when the operators go to high speed? Could the extra side-stream feed be a reason for the step change in motor load?
I am curious that there are only two speeds and wonder why the program does not ramp the motor speed up and down using the VSD to adjust throughput according to the product flow and motor current load. If you only need two speeds why have a VSD? Is it used for soft starting? It probably means the screw is started with a full load of dust in the trough after every stoppage. That would be a bad idea as it is sure to create huge start-up torque. The trough needs to be run-out of product every time and started empty. Maybe the operators won’t clean the trough out after a plant forced stoppage, but every start-up with an empty trough will extend the conveyor life by one more forced stoppage.
I would rather have the weighing conveyor put after the screw conveyor and before the mixer and so allow you to use the weighing conveyor as a variable flow control weigh feeder. That way the whole circuit can be controlled by the rate of feed the mixing tank can handle (provided that does not then cause disruption to the rest of the production process).
You say the section of pipe with the flytes is where the auger shaft failed, just on the other side of where the stub shaft is flanged to the pipe. The solid drive shaft did not break but the pipe wall sheared. When the break was repaired someone should have taken taken photos of the break in the pipe. It would have been very useful to get pictures of the break so we could look at the type of failure and understand what happened to the screw.
I noticed on the open trough photo that there was what seemed like pitting corrosion on the shaft flytes and trough. If pitting is also on the pipe this would be a stress raiser and could start the crack that became the break. You maybe could look at going to 316L stainless steel pipe and stub shaft if the problem was pitting corrosion creating a stress raiser (though stainless is inclined to work harden if it suffers cyclical high stress). Now that stress raiser has been mentioned one other possibility to cause a stress raiser is a bad weld with inclusions or under-cutting, or even the heat affected zone (HAZ) from a good weld. You said the break was not at a weld but how close to a weld is the break; is it near where the stub shaft was welded into the pipe or flange? The heat affected zone from a weld is the softest part of the steel and the crack that starts the break can begin in the HAZ.
I again looked at the photos you sent me and I believe that there is another serious overloading problem with the drive. The drive is a shaft mounted gearbox which is tied back to a solid connection on the ground with the torque arm and driven by belts from an electric motor located to one side. The self-weight of the gearbox and the reaction forces from the torque arm and pulley tensions must be placing a huge bending moment on the drive shaft (to this bending load you must also add the start-up torque force needed to break the friction of the flytes against the trough/dust/crust).
I quickly did the basic free body diagrams below of the situation at the drive end and along the shaft. It is clear that should the shaft break it will be between the drive end bearing and the first hanger bearing. This is the section of auger that will get the highest combined forces.

You need to get your engineering people to do some detailed engineering calculations and check how much combined bending and torsional load is on the drive shaft section between the drive end bearing and the first bearing hanger under a fully loaded start-up. I have a suspicion that you may need to get rid of the shaft mounted drive and install a direct in-line drive. With a direct-coupled drive there mostly will be torsional load and very little bending load.
I don’t know how hard it is to move the drive to the discharge end of the screw conveyor and make the auger pull the material through. By moving the drive to the outlet end and pulling material along the trough you move the bending forces to the end of the shaft where the torsional forces are least. The torque required to turn the flytes rises as the length of the trough increases since more flights and their rubbing area are in contact with the trough and bulk material. Though the motor matches the total torque created along the trough the shaft bending forces from pulling material through are now at the least stressed end of the auger shaft.
One other downside of pushing bulk material through a trough is the bending forces bow the shaft hard against the trough and cause more torsional frictional which the drive then needs to overcome. So the drive ramps-up the torque because the shaft is bowed and this extra force causes the shaft to bow harder agaist the trough, so the motor ramps-up the torque again to overcome the drag, only to bow the shaft more and need even more force to overcome drag, and so on continually.
A secondary benefit of dragging the fertiliser through is that you now have the whole shaft length along which to accumulate fatigue damage from torsional overloads of a blocked conveyor, so though the shaft will be over-stressed with each bog-down and cause the metal to yield the shaft will last longer between breakages because it can be twisted along more of its length before snapping.
You could of course change pipe wall thickness to XS or XXS thick pipe and have more material to take the combined bending and torsional loads. That is probably your easiest option. But by using thicker pipe you move the breakage point to another component or assembly on the screw conveyor. You will end up failing something else, like the gearbox, though probably less often. However it may be a far more expensive failure than a sheared auger.
Another possible quick fix to reduce the bending forces would be to move the connection point of the tie-rod up to be in-line with the drive pulleys’ center line projected from the motor shaft through the gearbox driver shaft and onwards to the building structure. Moving the tie-rod force to be in-line with the pulley tension force leaves just the gearbox/pulleys self-weight and the start-up torque for the shaft to handle. That reduction in force should make a big difference to the service life of the shaft. It will need to be a very strong steel mounting structure since there will be a big leverage force trying to rip the mounting out of the floor. Here again you need engineering calculations to design a sufficiently robust structural mounting.
I would be happy to do the machine loading and structural engineering calculations for a fee to cover my time if you want to, but I would need to get all the necessary dimensions and equipment engineering details from you to do that.
There are lots of engineering questions for you to consider before making a decision on how to best address the shaft breakage problem.
My best regards to you,
Mike Sondalini
Managing Director
Lifetime Reliability Solutions HQ
P.S. If you have maintenance engineering advice on industrial equipment maintenance, especially defect elimination and failure prevention of plant and equipment, or have made successful equipment reliability improvements, please feel free to send me your articles to post on this website. You can contact me by email at info@lifetime-reliability.com
Leave a Reply