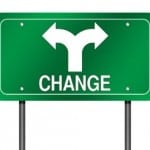
Why is it that Reliability Programs often fail and are not sustained? Bringing about such a change in a large organization is often one of the most difficult tasks that we undertake.
This undertaking requires a shift in mindset and in the ways people work. People love the status quo and are often afraid of the change. We must show them that there is nothing to be afraid of and that the change will be beneficial.
From personal experience, implementing Maintenance Planning and Scheduling at one site is completely different than trying to across a region. But the steps below will work regardless of the size of the change.
Here are 7 steps where we can focus our time on embedding reliability:
1. Change Management: Prior Planning Prevents Poor Performance. During this step, we must establish the need for change, and create a compelling reason to do so. We need to have something that will engage people and pull them in. Once we have the reason, we need to select a framework to manage the change program. I recommend ADKAR by Jeffrey M Hiatt, for its simplicity.
2. Engagement: We need to create engagement in the change at all levels of the business and across all departments. Reliability is jointly owned by operations and maintenance. As such we need operations to be as engaged as we are. This is where we use that compelling reason for change. It should be communicated by the change agents and the sponsors until everyone knows it as well as their own birthday.
3. Training: People are often afraid of what they don’t know. Training is a way to help overcome that fear. When training, we need to not only train on the new ways of working but on the why. During this time, we should be open to listening to the suggestions of the staff on changes. During this time, we should also be creating that sense of ownership and responsibility by using operators and mechanics to deliver the training. This leads to…
4. Responsibility: When people are involved in the creation and growth of a new process, they act as an owner of it. We can further this sense of ownership by giving responsibility away. Give people the responsibility to make decisions affecting their work area, or assign people to be responsible for the cleanliness of an area. Give responsibility and create owners
5. Rigor: With everyone trained and ready to go, we must ensure that we maintain the rigor to sustain the change. Often times you will see a change come on strong and then gradually decline over time. Rigor eliminates the gradual loss. We can sustain the change long after the initial push by ensuring that we adhere to standards and processes, and focus on the KPIs. A good indicator of this is to see how the 5s program has improved or declined over time.
6. Courage: Everyone has to be courageous during this period change and uncertainty. The operators and craft need to have the courage to challenge the status quo and change their way of working. The Supervisors, Managers and Execs, need to have the courage to have the tough conversations with people who are not performing as they should.
7. Reinforce: With everything in place, we need to continue to reinforce the importance of reliability and the compelling reason to sustain it. If something is not meeting the standard, we need to address it to ensure that we reinforce the importance of it.
Implementing a Reliability program is extremely difficult, as is any change. I hope you find these 7 steps helpful and will start to make the changes required in your operation.
Remember, to find success, you must first solve the problem, then achieve the implementation of the solution, and finally sustain winning results.
What was your main tool for embedding and sustaining reliability? What was your biggest struggle?
I’m James Kovacevic
HP RELIABILITY
SOLVE, ACHIEVE, SUSTAIN
Leave a Reply