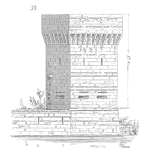
What you will learn from this article:
- How shaft packing works.
- What to consider when selecting and using shaft packing.
- Good installation practices.
- Proper commissioning of shaft packing.
Because compressed, stacked packing requires leakage to cool and lubricate, one would normally use packing on harmless products.
If used on environmentally unfriendly products or dangerous goods, the leakage must be collected and suitably treated to protect people and environment.
How compressed packing works
As packing is squeezed into place it fills the cavity in which it sits.
The packing will seal against the side and bottom of the stuffing box and on the shaft surface. When the shaft turns, it rubs against the packing and is wiped clean. Except for slurries, 70% of wear normally takes place in the first two packing rings nearest the gland throat.
The selection of suitable packing includes consideration of chemical compatibility of the components, the operating temperature of the process, the material of the shaft, whether additional lubrication embedded in the packing, such as graphite, will be useful whether a cooling and lubricating flush will be used.
Considerations when using packing
Because packing rubs on the shaft, friction is generated and wear occurs. The preferred methods of minimizing shaft friction are to:
- use a very smooth surface finish
- use a hardened rubbing surface (protect the shaft with a
hardened, replaceable sleeve if practicable) - use the slowest shaft speeds allowable
- ensure stuffing boxes are cylindrical; shafts are machined
round and run true to within 0.08 mm (0.003”), the gland throat clearance prevents packing extruding through it (maximum of 3% of packing width) - install a lantern ring to flush away contaminants
- install a lantern ring to feed a cooling and lubricating fluid to
the rubbing surface - select packing which helps heat to be removed
- select packing with friction-minimizing properties
- select a braid structure suited to the process fluid and pressures
– close-twined for gasses and high pressures. - for valves, the packing cross section must be a snug fit in the
stuffing box; for pumps packing cross section must have a slight (3%) clearance in the stuffing box.
Good installation practices
In order to minimize the extent of leakage from a packed gland do the following:
- cut each ring with a slanted end join as shown below
install the packing with each ring join staggered 90 degrees from the previous - set each ring individually in place with a tamping tool, or split hollow cylinder, turning the shaft occasionally
- push each ring hard up against the previous ring with no
gaps. This ensures the force generated by tightening the
gland follower is transmitted to all rings - lantern rings must line up with the flush port
- continue fitting rings until the gland follower projects 25%
to 30% of the stuffing box depth - a lantern ring flush must be a clean source and at a pressure
100 to 200 kPa above stuffing box pressure (about two-thirds the discharge pressure)
Commissioning shaft packaging
Commissioning a packed gland is a slow process. Proper bedding- in of the packing on rotating applications will take two to three hours to achieve.
Start with a generous leak and tighten the gland follower hand tight. Continue tightening evenly with a tool until the leakage flow levels off (even though the follower is being tightened). From then on make a half turn every fifteen minutes till the required leakage rate is achieved.
Monitor heat build-up in the wall of the stuffing box by hand so it rises no higher than warm to the touch.
Packed glands on pumps, when properly seated and adjusted ought to leak from five to twenty drops of product or flush liquid a minute.
Mike Sondalini – Maintenance Engineer
DISCLAIMER: Because the authors, publisher and resellers do not know the context in which the information presented in the articles is to be used, they accept no responsibility for the consequences of using the information.
We (Accendo Reliability) published this article with the kind permission of Feed Forward Publishing, a subsidiary of BIN95.com
Web: trade-school.education
E-mail: info@trade-school.education
If you found this interesting you may like the ebook Bulk Materials Handling Introduction ebook.
Leave a Reply