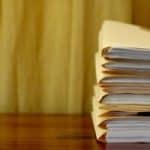
Utilizing Recognized Standards in Your Maintenance & Reliability Program
Imagine being able to easily share information across sites or even organizations. Or how about utilizing a risk management framework that is recognized and agreed upon by all in the organization. Benchmarking made easy? Standards enable this.
Why is it organizations spend countless hours developing a framework, templates, and a procedure for a routine activity? It provides standardization, and in turn reduces costs. What if we could have those same benefits, without all of the hours invested up front?
This is a reality, and it involves utilizing existing standards. These standards come from professional bodies (PEMAC, SMRP, PMI), or standards organizations (ISO, ANSI, IEEE). These organizations invest a tremendous amount of time developing and peer reviewing known best practices to develop these standards. So why not use them?
Which Standards Should I Use?
In the field of maintenance & reliability, there are some common standards which many find useful. Provided below is a brief list (If you click on an item, you may be taken to ANSI, and will have to enter the title there for a detailed description & pricing);
- ISO 14224 – Maintenance & Reliability Data
- ISO 55001 – Asset Management
- ISO 31000 – Risk Management
- SAE JA1011 – Reliability Centered Maintenance
- IEC 60812 – Failure Modes Effect Analysis
- SMRP Best Practice Guide
- PMBoK – Project Management Framework
- ADKAR – Change Management Framework
While some of these are frameworks, they are excellent resources in any maintenance & reliability professional’s toolbox.
Where Can I Look For Other Standards?
The first step in looking for other standards is to identify the need for a standard. Instead of writing one from scratch, start by looking for an existing one. They may not be free, but there are substantially less than that cost of developing one in-house.
Standards and best practice documents can be found by searching the Standard Bodies or Professional Bodies. But if you don’t know which body to start with, just start with a google search.
For example, if you are looking for a maintainability standard, don’t start developing one until you do a search. After doing a quick google search, I was able to find a risk management standard developed by ISO.
Finding standards could be tricky, but start here;
- American National Standards Institute – ANSI
- Institute of Electrical and Electronics Engineers – IEEE
- International Organization for Standardization – ISO
- American Society for Testing and Materials -ASTM
Next Steps
Your first step is to evaluate which processes could benefit from industry best practice. These may be processes you perform routinely or those that are not providing the expected return on investment.
Do a quick google search (if the relevant standard is not provided above or below) to find the standard(s) that are relevant to the process you identified.
Do not be afraid of the costs, even if it is $300, that is less than the cost of your maintenance engineer for a single day. How long would it take them to develop or revise your existing standard? Probably much more than a single day.
What do Once You Have The Standards
Once you have the standard, you can do a few things to ensure the organization gets the most value from it.
- First start by reviewing the standard, and determine what applies to your organization. This does not mean, removing anything you don’t want to do, but remove anything that is not relevant. There is a difference between the two.
- Determine how your process or data is different. Conduct a gap analysis to determine the gaps from the standard to your data or process
- With the gaps identified, determine what resources would be required to close the gaps.
- Prioritize those gaps based on the ease of implementation and the return of investment.
- Make the changes and start using the standard.
If you don’t implement the standard (whether it is a portion of it or the entire standard), there will be no benefit to the organization.
How many of your processes or data sets meet industry standards? Do you see a benefit to aligning with those standards? If not, I would be curious to find out why. Please leave a comment and let me know.
Remember, to find success, you must first solve the problem, then achieve the implementation of the solution, and finally sustain winning results.
I’m James Kovacevic
Eruditio, LLC
Where Education Meets Application
References:
- ISO 14224 – Maintenance & Reliability Data
- ISO 55001 – Asset Management
- ISO 31000 – Risk Management
- SAE JA1011 – Reliability Centered Maintenance
- IEC 60812 – Failure Modes Effect Analysis
- SMRP Best Practice Guide
- PMBoK – Project Management Framework
- ADKAR – Change Management Framework
- American National Standards Institute – ANSI
- Institute of Electrical and Electronics Engineers – IEEE
- International Organization for Standardization – ISO
- American Society for Testing and Materials -ASTM
Leave a Reply