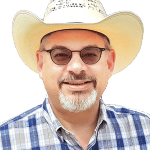
Guest Post by Joseph Paris (first posted on CERM ® RISK INSIGHTS – reposted here with permission)
As very young children, we had an instinctive need to be very close to our parents – feeling a great deal of anxiety, even a sense of abandonment, if they were not within our sight. As we grew older – and whether it was geographically, intellectually, or psychologically – we would become more comfortable with greater distances from what we felt were our basic truths, but almost always as stepping stones and rarely great leaps.
Think of early commanders of sailing ships always keeping sight of land until traveling ever greater distances was more predictable because of maps and navigation techniques and tools.
From the time Humans learned to sharpen stones to help with the hunt and the chores then gaining the wisdom to attach them to sticks to improve their effectiveness in the hunt, to harnessing the wind and eventually the atom to leverage the energies contained therein, we have been seeking ways of improving our lives. The one common discipline that runs through all of these stepping-stones of advancement is the notion of Continuous Improvement – the increase of velocity and predictability with less human effort.
As it is with the notion of Lean which, it can be argued, started with Henry Ford and the assembly line and was leveraged on a mass industrial scale during World War II.
But after World War II, there was a divergence in the way companies were run in the West as compared to the East which was largely based on the cultural differences in the structure of the social fabric. In the West, the relationship between employer and employee was largely one of command and control – about the self. Whereas in the East, this relationship was inclined to be more collaborative and about the community. This difference meant that the ideas of how a modern business might operate – in an increasingly global marketplace – progressed faster in the East than in the West.
Just as the Central Planning of nations that practiced Communism proved inferior to the Distributed Planning of nations that practiced Capitalism; the practice of Command and Control in business proved inferior to those nations who were Collaborative.
So it is with the stepping-stones of the journey that is Lean. The real question, and challenge, is whether Lean is an inclusive discipline or an exclusive discipline?
For instance, do those that embrace Six-Sigma as a means to Continuous Improvement run contraire to the aspirations that is Lean? How about those who are disciples of the Theory of Constraints? Are PDCA, DMAIC, and OODA incompatible with one another? How about you, personally? Do you ever find yourself arguing the merits of one approach or set of tools versus the other? Is it because you are correct or is it because you like to stay close to your parents as you did when you were a child – because it’s comfortable? What if nobody was right or wrong – yet everyone was right and wrong?
We talk about “creating a pull” in the operations of our business. What if we tried to “create a pull” when it came to opportunities for improvement – with the nature of the opportunity creating the pull on the various tools, approaches, and “isms” necessary to realize the opportunity without prejudice?
After all, if Lean is about improvement, then as it exists today must change for tomorrow as we move forward onto the next stepping-stone.
by Joseph Paris
Paris is the Founder and Chairman of the XONITEK Group of Companies; an international management consultancy firm specializing in all disciplines related to Operational Excellence, the continuous and deliberate improvement of company performance AND the circumstances of those who work there – to pursue “Operational Excellence by Design” and not by coincidence.
He is also the Founder of the Operational Excellence Society, with hundreds of members and several Chapters located around the world, as well as the Owner of the Operational Excellence Group on Linked-In, with over 60,000 members. Connect with him on LinkedIn or find out more about him here: www.JosephParis.me/card
Leave a Reply