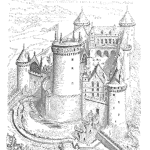
Suppliers always declare their commitment to the highest standards of quality as a core value, but many have trouble living up to that promise.
I can’t tell you how many times I’ve visited suppliers who proudly display their framed ISO certificates in the lobby yet suffer from persistent quality problems that lead to higher cost and schedule delays.
Here’s how you can tell if they’re really serious:
1. Do they have an on-going program of quality improvement, or do they wait until you complain? Do they have an understanding of the sources of variability in their value stream, and can they explain what they’re doing to reduce variability without being asked to do so? Look for any testing and measurements that occur before outgoing inspection. Award extra credit if the supplier can show process capability studies and control charts. Ask what they’re doing to analyze and reduce the internal cost of quality (scrap and rework).
2. Do they accept responsibility for misunderstandings regarding specifications and requirements? Or, do they make a guess at what you want, and later insist they just did what they were told? Quality means meeting or exceeding customer expectations, and a supplier who is truly committed to quality will ensure those expectations are clear before they start production.
3. Do you find defects when you inspect their first articles or samples from their first shipment? If the supplier can’t get these right when there’s no schedule pressure, you should have serious concerns about their ability to ramp up to your production levels. By the way, if you’re not inspecting a small sample of first articles, you’ll have to accept at least half of the blame for any subsequent quality problems.
4. Has the supplier ever warned you of a potential quality problem discovered on their side, or do they just hope that you won’t notice? I realize this is a sign of a more mature relationship between supplier and customer, but a true commitment to quality means that the supplier understands their role in your value stream, and upholds your quality standards without being asked.
Conclusion
Ultimately, you will get the level of quality you deserve, depending on what suppliers you select and the messages you give them. You may be willing to trade quality for lower unit cost, shorter lead time, or assurance of supply.
The real question is: What level of quality do you need? What level of poor quality can you tolerate?
Related:
Subcontracting Quality (article)
What to Specify with Suppliers to Achieve Reliability Goals (article)
Reliability Questions to Ask Your Suppliers (article)
Leave a Reply