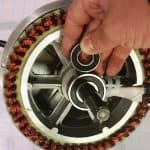
We, as developers, create designs that we call “our own.” Rarely are the materials for our in-house manufacturing process raw steel, rubber, and glass, like Henry Ford had feed into the Ford factory in 1930. Our manufacturing process receives a mix of materials and fully functional sub assemblies from other technology companies. It’s unlikely the PCB electronic components, bearings, motors, gears, drivetrains, sensors, power supplies, harnesses are ours. Why would you design any of these with so many options available made by specialists? This results in us having little input or control in the development and demonstrated reliability of our entire product.
After having spent significant resource on measuring and improving reliability on our portion we then send the product off to production knowing only part of the story. To address this we could fully evaluate the supplied assemblies and components we source. This does negate some of the value of using supplier components because now we are investing significant resource in the qualification, and likely development, of their products.
The answer is to have teared levels of of DfR engagement with suppliers. These are the levels I believe work.
- The supplier has done a full DfR program including statistical reliability statements based in test programs. You as the customer are using the product per their specifications which ensure the test results and reliability statements are valid. This is the most clean cut scenario. It is important that your team invest in acquiring the suppliers reports and data on the product. This information is then incorporated into your development program documentation along side your in-house reports.
- The supplier has done DfR and a reliability testing program, but the use-case and environmental conditions do not match your application. The solution is qualification testing in-house or at the supplier using your product use-case and environmental specifications. In many cases the supplier yields benefit as well with this engagement. They will have qualified their product to higher, or my diverse, conditions that potentially increases their customer base and market value.
- The supplier has not done any DfR practices in the development process. There are two paths for this scenario. The first is to investigate if their is a supplier of an equivalent product that does do DfR in the product development process. If this is not the case and your current supplier has a proprietary/cutting edge technology then a path of cooperative engagement may be best. This often includes the supplier operating like an extension of your reliability and design team. You as the customer may pay the supplier directly as compensation for their investment in creating and executing a reliability program. The arrangement may be that your investment is non-recoverable engineering cost. Alternatively it may be that you have exclusive rights to the newly qualified and improved product for a period of time.
What is important is the clear mandate that your team owns the reliability of the entire product regardless of percentage of sourced technology.
-Adam
Leave a Reply