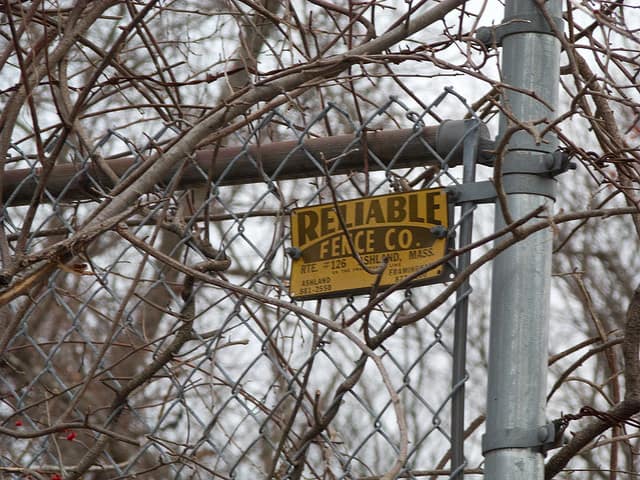
Supply chain MTBF vs Reliability requirements

Let’s say you have a reliability goal for your product of 95% survive 2 years in an outdoor portable environment with the primary function of providing two way communication. There is an engineering reference specification detailing the product functions and requirements for performance. There is a complete document of environmental and use conditions . And you have similar detailed goals for the 1st month of use the expected useful life of 5 years.
And you need to buy subsystems from a range of suppliers. They:
- Don’t know what to do with the allocated reliability goal (all four parts clearly stated)
- Consider production yield as good enough
- Have to buy parts and elements from their suppliers.
They continue to ask their suppliers for reliability measures and accept MTBF values.
What can you do to influence the suppliers of your suppliers?
Constraints
Contracts, purchase agreements and meetings have a limited reach into the supply chain. You suppliers may have long standing contracts with their suppliers. They most likely have already designed and sources the components for the subsystem of interest. They have other customers that are not asking for anything more then MTBF.
Another consideration is the increasing reliability requirements for components on subsystems within your system. The company making capacitors for use on your power supply in your product may be able to meet the allocated reliability objective specific for the capacitor, yet the number of samples or duration of testing are probably well beyond the capabilities of the capacitor qualification.
Besides capacitors don’t fail. Right?
Everything Fails
One of great things about reliability engineering is eventually and often unexpectedly everything fails. Running tests that do not fail and demonstrate the expected failure mechanism might be part of the issue.
If the capacitor vendor would run 40 units to failure using three or so sets of conditions, designed such that they could validate a time to failure model, we would be able to understand
- What will fail
- When it will fail
- Why it fails
Much better than a tabulated set of (bogus) MTBF values.
Possible Solutions
Require reliability testing that includes failures along with failure analysis evidence confirming the root cause of the failures. Ideally this would include every component in the system. Realistically it will include critical components, high risk components or new technologies.
Instead of asking for and accepting MTBF values, ask for and accept a reliability case. Ask for evidence and a compelling fundamental understanding of what is expected to fail and when. Ask for and expect to learn the process, component, and application elements that would lead to failure.
Instead of accepting a list of standards based test passes, ask for and expect to learn about time to failure distributions and how they change as applied stresses change.
Instead of waiting for something to failure to conduct failure analysis. Ask your supply chain to provide a similar level of detail on what is expected to fail. Include root causes of their design, assembly process and especially of their supply chain.
In short — ask for real reliability information.
Leave a Reply