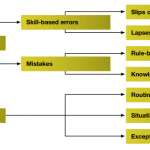
Equipment is described as reliable when it functions as designed without failure. Admittedly, equipment failure of any kind is quite inconvenient especially in fast-paced environments like the manufacturing sector. However, the consequences of failure – if it were to occur – go just beyond the usual inconveniences of unplanned downtime, lost productivity, lost revenue, etc. All these are bad enough, but should equipment failure cause injury or fatality, recovering from the consequences could become an uphill task.