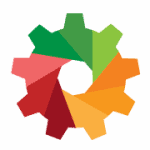
When designing equipment and processes, engineers leave a safety margin that ensures equipment remains functional when a fault or defect is affecting it partially or wholly. Minor defects affecting production assets should not cause immediate breakdowns. A fault-tolerant system remains operational for predetermined intervals before undertaking corrective measures. Faults affecting the operation of different systems emanate from more than a single source. [Read more…]