When was the last time you were involved with a regulatory body? I can remember a time when a millwright was involved in an incident in our maintenance shop. He was using a 20″-disc grinder when the piece of steel he was grinding got caught and pulled his hand into the grinding wheel. He was off for a quite a few weeks, but he did not sustain any long-term injuries.
[Read more…]
Benefits of Manufacturing Maintenance Software

Maintain equipment, minimize downtime, meet production demands, manage inventory levels, monitor staff productivity, comply with regulatory standards, etc. etc. The list of maintenance demands in a manufacturing plant is nearly impossible to meet without the help of computerized maintenance management systems (CMMS). Manufacturing CMMS software automates the process of maintaining assets to help simplify operations, maximize uptime and control costs.
Many manufacturing plants are relying on outdated systems or maintenance spreadsheets to keep tabs on their equipment and other important aspects of production. In doing so, they run the risk of premature equipment failure, production lags, increased downtime and, ultimately, the loss of business. Consequently, competitors utilizing modern manufacturing CMMS software are more successful.
Components of an Effective Maintenance System
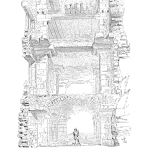
If you are ever in the fortunate position of developing a maintenance system from the beginning, the list below will help you focus your efforts. Maintenance systems in small business, develop by default and without much forethought. This list puts together, in one place, the important components of a workable maintenance system. [Read more…]
Uptime: Managing Failures Before They Occur
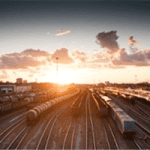
Being proactive with your assets is all about managing failures before they occur. You can reduce or eliminate the consequences of failure by forecasting what is likely to happen and deciding in advance about what to do about it. The advantage to doing this is that major business impact due to equipment breakdown can be avoided. High performing companies manage proactively – they foresee and avoid problems. It’s good for business! [Read more…]
What is Criticality Analysis? How Does it Work?
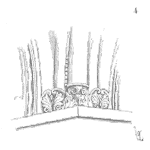
Understanding the risks allow effective mitigation plans to be put in place
Where is your biggest risk to the site? If you can’t answer that, than your maintenance program is most likely not adequate. As previously discussed, an effective maintenance program must align with business and its needs. A criticality analysis allows the site to understand where there are risks that must be managed. [Read more…]
Is Your Maintenance Program Aligned With The Business?
Providing the right level of service to production will ensure the profitability of the business.
Using a Business Needs Analysis will ensure that your maintenance program is on the same page as the goals of the business. Often times the two are not aligned, which leads to excess costs for the business, reducing the ability to be profitable. For example, does your operation require 99.9% reliability? It would be nice but that level of reliability is extremely difficult & costly to achieve. Think of the various industries that require that level of performance. NASA, the Armed Forces, Nuclear Power, etc. require 99.9% reliability and to achieve so, the effort in design and in operation is extremely intensive. [Read more…]